5s In Machining Workshop
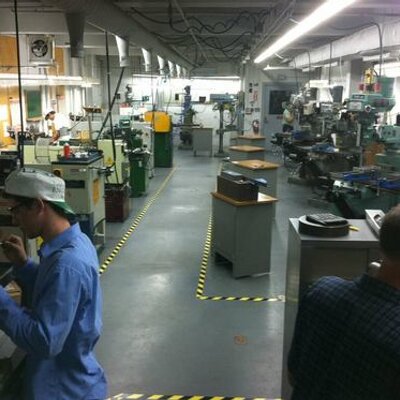
Thayermachineshop At Machine Shop We Follow 5s Safe Work Practice This Practice Helps Us To Better Assist Students While Ensuring T Co Uxkycrjei1

5s Explained

How The 5 S S Of Lean Manufacturing Helped Our Custom Cnc Machine Shop Fitzpatrick Manufacturing Co

Machine Shop Wikipedia

Lean In The Small Shop Plant Management

Pryme Group S Ga Scotland Launches Fast Make 5s Team Pryme Group
Description 5S methodology has been introduced and perfected by Toyota in order to make waste visible and eliminate it 5S, a system of visual cues that helps reduce waste and achieve more consistent operational results through maintaining an orderly workplace, has been widely used in all sorts of organizations, from manufacturing to health care, from military to financial institutions.

5s in machining workshop. 5S Manufacturing Checklist This 5S manufacturing checklist can help you identify unnecessary items in the manufacturing site The quality audit checklist for manufacturing ensures materials, products, tools, and equipment are properly labeled, cleaned, organized, and stored in the proper location. Manding machining The theoretical suitability of 5S, for implementation in to the company, was examined in this work A comparison to other development programs showed that 5S is a functional solution to current problems in the company The 5Soperating model was pushed through in three well chosen pilot targets. Jan 10, 21 Explore janisleilands's board "5S" on See more ideas about lean manufacturing, visual management, lean six sigma.
Essentially, 5S requires just these five steps sort, set, shine, standardize and sustain If a business engages the entire team and begins to address each one on one project or manufacturing line, it can work through the process, resolve any issues and then extend the approach. History of 5S 5S is believed to have started as early as the 16th century with the Venetian shipbuilders in Venice, Italy They used quality inspection techniques in an assembly line approach to manufacturing ships for the royal navy Fast forward to postWorld War II, the Japanese automotive manufacturing industry gave way to the formal birth. 2 Stick to the „5S‟ rules for proper workplace management 3 Encourage the participation of all, for consistency in „5S‟ activities 4 Perform „5S‟ activities periodically 12 Organization Introduction Menon Piston Ltd, Maharashtra, India inaugurated in 1969 MPL is a total engineering solution.
The 5S methodology was born at Toyota in the 60s under an industrial environment to achieve better organized, tidier, and cleaner workplaces to increase productivity and to obtain a better working environment The 5S methodology has been widely spread, and many companies and organizations are implementing it worldwide Although it is conceptually simple and does not require a complex training. Generating a 5S Checklist for Manufacturing The 5S practice is a technique used to establish and maintain quality environment in an organization The original concept was developed by Osada in the early 1980s The acronym 5S stands for the five Japanese words seiri (organization), seiton (neatness), seiso (cleanliness), seiketsu (standardization), and shitsuke (discipline). Material This paper focuses on work in CNC machine cell area, where the cell produces the gearbox housing unit Already lean tools like 5S, continuous flow, justin time, overall equipment effectiveness are implemented in this CNC manufacturing cell The study focuses on work.
ABSTARCT 5S is an important tool within Lean Manufacturing, developed as part of the Toyota Production System (TPS) and Total Productive Maintenance (TPM), it is a highly effective and simple tool. 5S is an organisational method describing how to organise a workspace It is one of the most widely adopted techniques from lean manufacturing toolbox The main objective of 5S is to create a clean, orderly environment where there is a place for everything and everything is in its place 5S makes it easier for people to do this without wasting. 4=flawless, no deviations ever).
Workshop Deliverable Seeing is Believing The workshop is designed to provide theoretical knowledge about 5S along with the handson experience when done on the shop floor In the two days of the workshop, a model area will be chosen and steps 1, 2, and 3 of 5S will be demonstrated in the designated area Training Contents Introduction. The 5S’s (Sort, Set in Order, Shine, Standardize, and Sustain) are rough translations from the original Japanese terms referring to a process to optimize workplace organization The premise for the 5S’s is that a lot of improvements and inefficiencies can be made by having a clean, organized and efficient workplace. QualityOne International 1333 Anderson Road Clawson, MI Ph Fx.
Workshop Overview In this workshop each participant is provided with two, handson “real world” simulations on how to facilitate and maintain a successful 5S Program Each simulation will have a “Learn by doing” approach and cover all aspects;. Workshop Overview In this workshop each participant is provided with two, handson “real world” simulations on how to facilitate and maintain a successful 5S Program Each simulation will have a “Learn by doing” approach and cover all aspects;. Once an organization determines the 5S strategies are a good fit for the company, they need to start planning out how to implement 5S Proper implementation will require physical changes to the facility, as well as training employees and other parties to operate in accordance with the 5S methodology It can take quite some time before 5S is fully implemented, but there will be significant.
‘5S’ in simple terms is a Japanese technique consisting of five ‘S’terms namely Seiri (sorting), Seiton (set in order), Seiso (shine), Seiketsu (standardize) and Shitsuke (sustain) having a deep sense for managing the work place. Proble m state ment 5S practice is one of the techniques to improve quality environment, health and safety at the wor kplace Evaluation of 5S practice can be done through implementation of 5S. 6S manufacturing is an approach to production processes that integrates the 5S principles with safety For example, manufacturers that practice 6S in manufacturing considers the safety of workers, their working conditions, and the equipment they use when implementing lean programs and conducting 6S audits.
What is 5S ?. 5S is a formulaic method you can use to straighten and organize a work area Using 5S reduces waste (a fundamental goal in lean manufacturing), improves safety (see our article on Lean 6S Safety ), and otherwise improves your production process and work environment 5S is called 5S because their are 5 steps and each step begins with the letter “S” (and/or the sound “s”). 5S is a fundamental first step for any manufacturing company, wishing to call itself world class We will understand this with step by step approach of its deployment The 5S program mandates that resources be provided at the required location and be available to support work activities.
Sort, set in order, shine, standardize and sustain. 5S Manufacturing Checklist This 5S manufacturing checklist can help you identify unnecessary items in the manufacturing site The quality audit checklist for manufacturing ensures materials, products, tools, and equipment are properly labeled, cleaned, organized, and stored in the proper location. – Muri overburden, unreasonableness or absurdity – Mura unevenness or inconsistency, primarily with physical matter and the human spiritual condition – Muda activity which is wasteful or doesn’t add value.
Once an organization determines the 5S strategies are a good fit for the company, they need to start planning out how to implement 5S Proper implementation will require physical changes to the facility, as well as training employees and other parties to operate in accordance with the 5S methodology It can take quite some time before 5S is fully implemented, but there will be significant. (examples machine parts which may cause cut, crush or other injuries, moving parts such as gears, pulleys and chains) started 5S’ing and colorcoding your facility Each kit contains an assortment of our most popular floor and workbench marking supplies Kits that include a Brady portable label printer are also. 5s is based on five Japanese terms all starting with s (the English version also start with S), that represent steps towards the final aim, which is to sustain workplace efficiency Sort Separate needed tools, materials, and instructions from those not needed Remove everything that is not needed in the work area.
With more than 106 million unique visitors over the last year, Practical Machinist is the most visited site for metalworking professionals Practical Machinist is the easiest way to learn new techniques, get answers quickly and discuss common challenges with your peers. Why You Should Register for 5S Training & Certificate In the 5S Training (Single Module), you’ll learn the basics of these tools and techniques and continue building your problemsolving muscles What You’ll Get (Certificate, PDUs/CPEs) 5S Manufacturing Assessment Template & Example;. From the concept of lean, many tools have been devised to assist in reaching a goal of a more lean manufacturing production process, and one of the best for organization is the 5S system 5S comes from 5 Japanese terms that, when combined in a particular order, help a shop become more visuallyorganized.
What does 5s stand for?. This is a 5s training video for our cnc machine shop. 5s Checklist for Manufacturing In a manufacturing environment, generating the 5S in practice can bring in results that could considerably raise the environmental performance in line with the improved housekeeping and health & safety Generating the 5S checklist for manufacturing prior to auditing comes in different forms.
60 5s Checklist for Manufacturing 50 60 5S Checklist for Tool Room 51 60 TPM Checklist 52 Sustain Periodic Reviews 53 1 Removing unnecessary items 2 Storage of cleaning equipment 3 Floor cleaning 4 Bulletin boards 5 Emergency access 6 Items on floor 7 Aisleways markings 8 Aisleways maintenance 9 Storage and arrangement 10. The 5S is a methodology aimed at optimizing the productivity and reducing waste at the factory It makes use of visual cues and an orderly workplace to achieve consistent results The 5S is implemented by small teams working together to achieve a higher goal of efficiency It can be performed in any company that does manufacturing in the USA. 1 Presentation of the 5S approach 2 Description of the 5 steps 3 Visual management 4 Workshop animation description 5 Key Success Factors to maintain 5S results and to set up continuous improvement 6 5S workshop on pilot project on a working area of your choice 7 Action plan with remaining tasks to be performed on the Pilot Project.
5S is one of the first tools that can be applied in a company that is starting down the path of the continuous improvement culture A 5S implementation helps to define the first rules to eliminate waste and maintain an efficient, safe, and clean work environment. The Origins of 5S – 5S & Lean Manufacturing 5S began as part of the Toyota Production System (TPS), the manufacturing method begun by leaders at the Toyota Motor Company in the early and midth centuryThis system, often referred to as Lean manufacturing in the West, aims to increase the value of products or services for customers. You get 5S training workshop material containing a 5S PPT PowerPoint Presentation of foundational 5S knowledge, and a 5S game people play that puts them into a 5S Simulation where they continually improve and learn the value of 5S The 1day 5S training workshop comes complete with the 5S PPT presentation, a 5S training course workbook with 5S activities, and a powerful 5S simulation that your people play, and wins them over to wanting 5S workplace management.
It's relatively easy to make a 5S audit checklist of each value stream, work cell, machine or office in any operation Conducting the audits is easy What's not easy is having the high expectations and discipline by the leadership to set the proper stage with communications, standard work, assignment of specific responsibilities, relentless. 5S Manufacturing Checklist This 5S manufacturing checklist can help you identify unnecessary items in the manufacturing site The quality audit checklist for manufacturing ensures materials, products, tools, and equipment are properly labeled, cleaned, organized, and stored in the proper location. • 5S activities are to create good working environment through reduction of “ Muri”, “Mura”, and “Muda” • It help to have a basis of strong management of workplace • What is “Muri”, “Mura”, and “Muda”?.
A 5S can be applied to any work environment It could be a supply/store in a hospital, a repair truck for a telecom company, a CSR desk/work area in a call center, the baggage claim area of an airline or a laptop computer. In actuality, the principles within 5S were being utilized decades before by Mr Henry Ford It has been reported that prior to 19, Mr Ford was using CANDO in his manufacturing processes The acronym CANDO stands for Cleaning up, Arranging, Neatness, Discipline and Ongoing improvement. Both the practice and the benefits of 5S are abundantly evident at this 65person shop located deep in the piney woods region of East Texas 5S has prepared Merritt Tool for lean manufacturing More accurately, 5S is propelling this shop toward lean manufacturing.
5S comes from 5 Japanese terms that, when combined in a particular order, help a shop become more visuallyorganized For example, if we wanted to “5S” a woodshop, we would need to break things down into these 5 S’s Sort, Set in Order, Shine, Standarize, and Sustain. I am often asked for suggestions on how to make a 5S program (the sort, set in order, shine, standardize and sustain program for improving workplace organization) really work as opposed to becoming just another “program of the month ” It’s an interesting question. Introduction to 5S Training Workshop Welcome to the oneday 5S training course by Lifetime Reliability Solutions Introduction to 5S 5S is workplace management where the work area and workplace are organised and ritualised to minimise the loss of time and the use of movement Originally part of Lean manufacturing philosophy (also known as.
Sort, Set, Shine, Standardize, Sustain — these are the 5S system’s basic steps to workplace organization and standardization Based on a simple set of visual cues, 5S/Visual Management helps you quickly locate tools, materials, information and quantity limits, identify issues before they become problems and create ownership for your operators. The Ultimate Guide to Improving Machine Shop Efficiency Making everything work together synchronously and efficiently is a balancing act Megan R Nichols Jun 28, 17 Modern machine shops can be compared to the complex parts they manufacture, with a number of moving parts, all of which require synchronous activity to achieve maximum. 5S BASIC MANUAL Table of contents Since the establishment of a healthcare services quality improvement workshop in 04, the Ministry of Health (MOH) has been striving for the improvement under the initiative of chiefs of relevant agencies Several Quality Assurance Programs (QAPs) are introduced to.
5S Visual Workplace Organization for Manufacturing and Services Workshop Description 5S Visual Workplace Organization describes a systematic approach of how to organize a workspace or area for efficiency and effectiveness by identifying and storing the items used, maintaining the area and items, and sustaining the new order. Mar 2, 17 Explore Vipul Vikas Singh's board "5S Ideas" on See more ideas about lean manufacturing, visual management, kaizen. 23 5S checklists, schedules and routines are defined and being used 24 Everyone knows his responsibilities, when and how 25 Regular audits are carried out using checklists and measures S5 – Sustain SHITSUKE 26 5S seems to be the way of life rather than just a routine 27 Success stories are being displayed (ie before and after.
While some Lean Six Sigma (LSS) practitioners consider 5S a tool, it is more than that 5S, abbreviated from the Japanese words seiri, seito, seiso, seiketsu, shitsuke, is not just a methodology, it is a culture that has to be built in to any organization which aims for spontaneous and continuous improvement of working environment and working conditions It involves everyone in the organization from the top level to bottom. Sort, set in order, shine, standardize and sustain. 5S WORKPLACE ORGANIZATION 5S is one of the most widely adopted techniques from the lean manufacturing toolbox Along with Standard Work and Total Productive Maintenance, 5S is considered a "foundational" lean concept, as it establishes the operational stability required for making and sustaining continuous improvements.
5S Transactional Assessment Template & Example. (examples machine parts which may cause cut, crush or other injuries, moving parts such as gears, pulleys and chains) started 5S’ing and colorcoding your facility Each kit contains an assortment of our most popular floor and workbench marking supplies Kits that include a Brady portable label printer are also. This is a 5S audit checklist for manufacturing companies There are a total of 25 evaluation criteria spanning the 5S principles Each criteria is evaluated against a fivepoint scale (0=we constantly deviate;.
5S, sometimes referred to as 5s or Five S, refers to five Japanese terms used to describe the steps of the 5S system of visual management Each term starts with an S In Japanese, the five S's are Seiri, Seiton, Seiso, Seiketsu, and Shitsuke In English, the five S's are translated as Sort, Set in Order, Shine, Standardize, and Sustain. Originally developed by Hiroyuki Hirano for manufacturing companies in Japan, the principles of 5S translate well to the laboratory, the repair facility, and even the corporate office Almost any work environment will benefit from the structure and efficiency this model provides 5S is sometimes called the five pillars because just like the. History of 5S 5S is believed to have started as early as the 16th century with the Venetian shipbuilders in Venice, Italy They used quality inspection techniques in an assembly line approach to manufacturing ships for the royal navy Fast forward to postWorld War II, the Japanese automotive manufacturing industry gave way to the formal birth.
ABSTARCT 5S is an important tool within Lean Manufacturing, developed as part of the Toyota Production System (TPS) and Total Productive Maintenance (TPM), it is a highly effective and simple tool. After initial training in 5S basics, workshop participants from “outside” companies and host organizations divided into project teams at each of the three host locations Selected 5S team activities and results follow Bison Gear and Engineering Corporation Bison Gear aimed to benefit from a 5S team’s evaluation of a CNC machining work.

The Three Pillars Of Reliable Machine Shop Productivity Modern Machine Shop
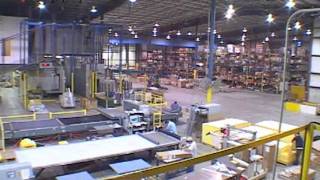
5s Explained
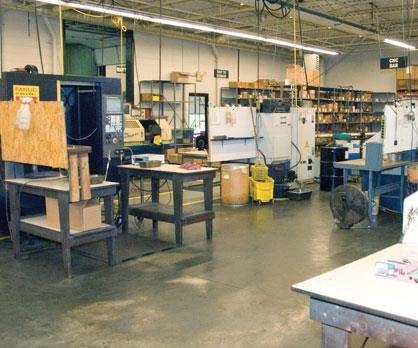
From Job Shop Chaos To Lean Order Modern Machine Shop
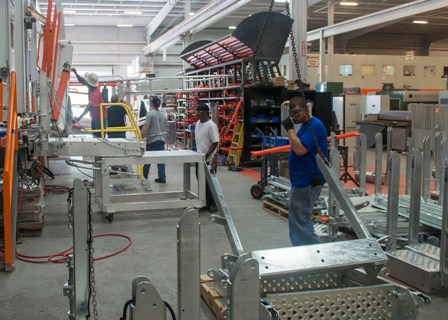
Plant Engineering Safety Is It The Sixth S In A 5s System

5s Lean Manufacturing

How To Apply 5s Method To Improve Shop Efficiency 18 12 06 Snips

3 Tips To Cross Functional 5s Projects Leancor A Transplace Company Leancor A Transplace Company
Detail Imbach Cie Ag

Machine Shop Wikipedia
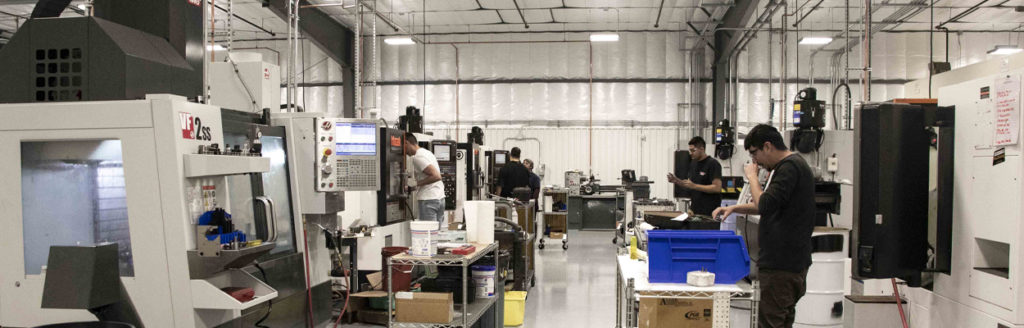
Two Keys To Lean Implementation In High Mix Low Volume Job Shops Agm Precision Machining

Learn And Implement Lean A Similar Lean 5s Tei Transformation Can Happen To Your Shop Floor Before Lean Implementation After Lean Implementation Click On The Photographs For A Big View More Photos Albs Undertakes Training

Boston Sheet Metal I Best Metal Manufacturer Expertise And Equipment To Scale With Your Business

Practical Machinist Largest Manufacturing Technology Forum On The Web

Getting Started With The 5s System 5s Implementation Plan Graphic Products
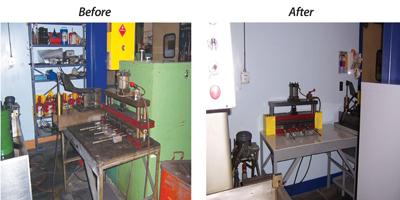
5s Or 6s What S The Safe Choice

Getting Started With The 5s System 5s Implementation Plan Graphic Products
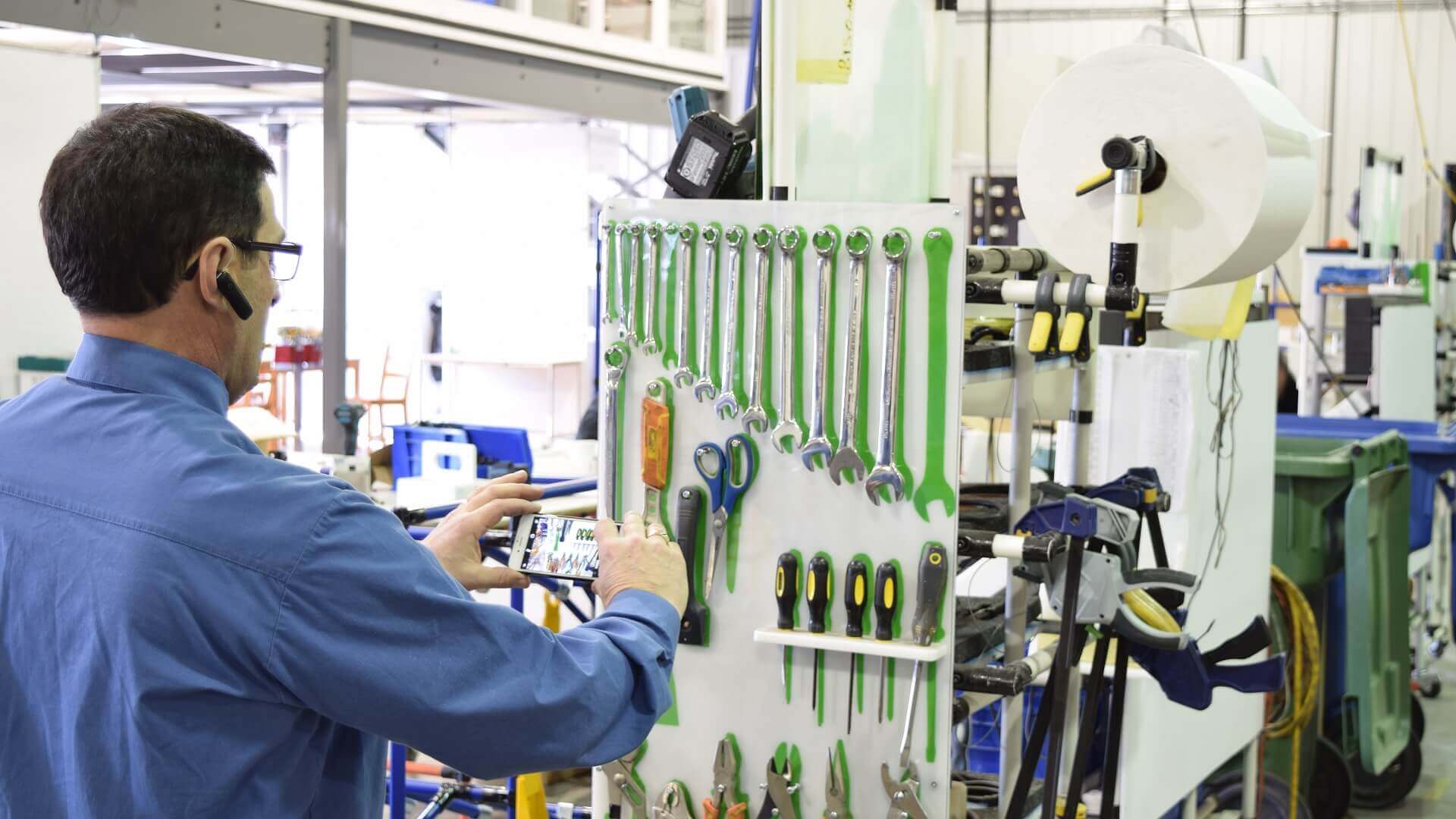
How To Do A 5s Audit With Your Iphone Flexpipe
.jpg)
Advanced Forming Research Centre Afrc 5s Materials Store Machine Shop University Of Strathclyde
Opep 5s In Manufacturing

3 Ways Your Organization Can Undertake A 5s Audit Izimage
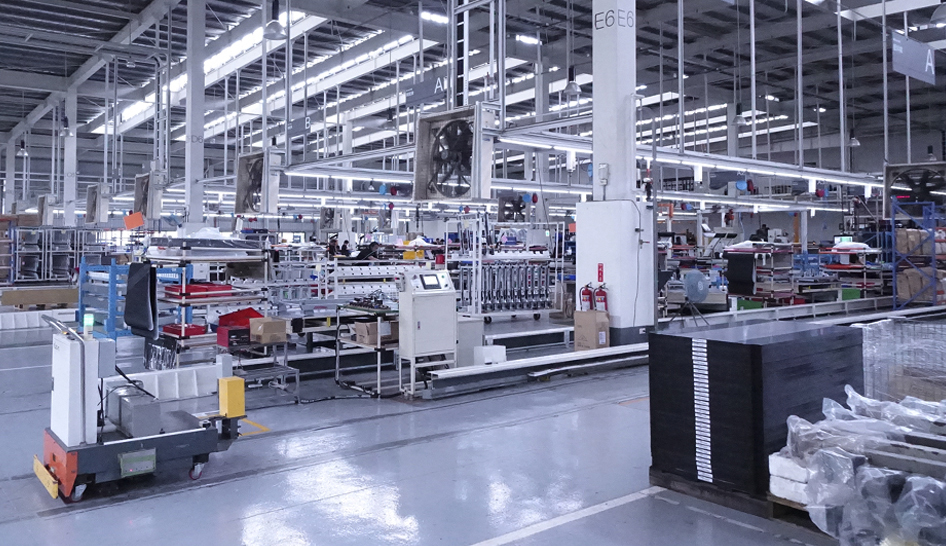
How Your Health Club Can Profit From The 5s Method Ihrsa

5s Program A Quality Tool Or Good Housekeeping
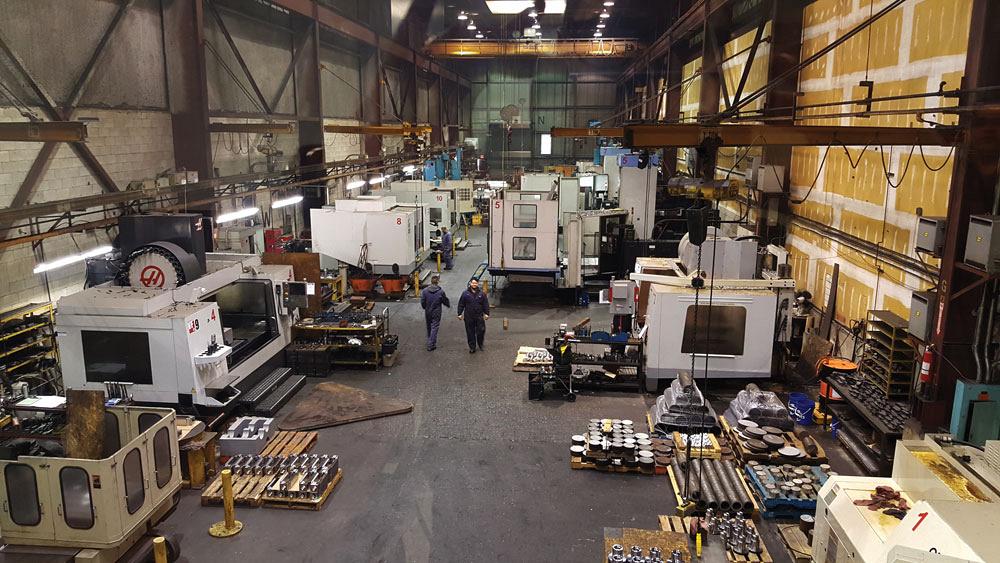
What Keeps You Up At Night

5s Lean Resource Center Stop Painting Com

Introduction To The 5s Concept Uttana Com
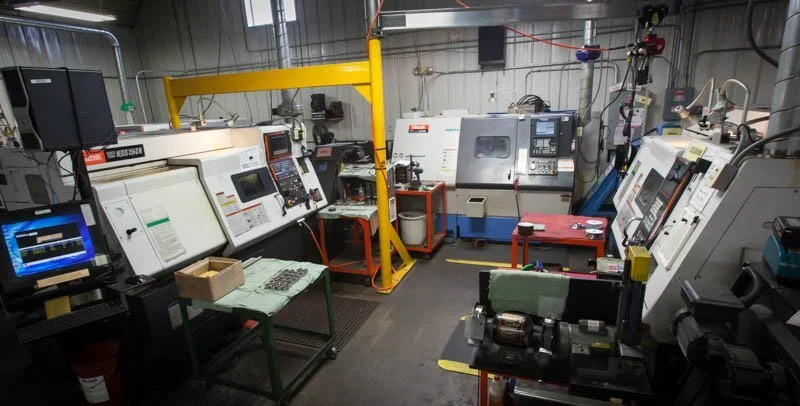
5s Machining Mrs Machining Milling Turning Augusta Wi
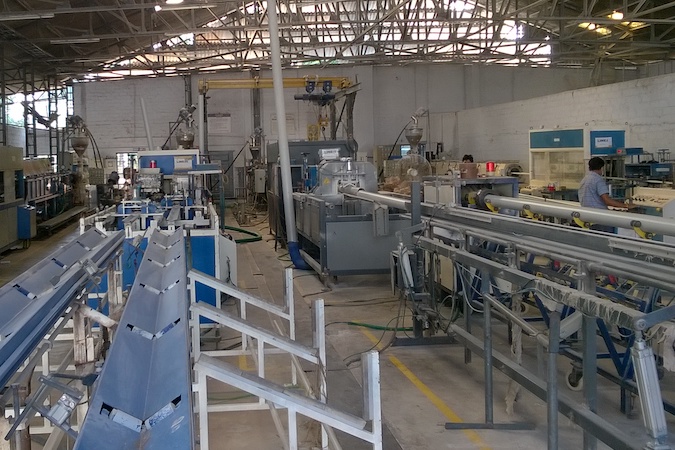
5s Implementation In Kelachandra Pipe Industries And Fittings Kerala Hash Management Services Llp

Amazon Com The 5s Playbook A Step By Step Guideline For The Lean Practitioner The Lean Playbook Series Ortiz Chris A Books

Learn And Implement Lean A Similar Lean 5s Tei Transformation Can Happen To Your Shop Floor Before Lean Implementation After Lean Implementation Click On The Photographs For A Big View More Photos Albs Undertakes Training

Zen Cart The Art Of E Commerce Lean Manufacturing Workstation Workshop Organization

Improve Workplace Safety With 5s Realsafety Org
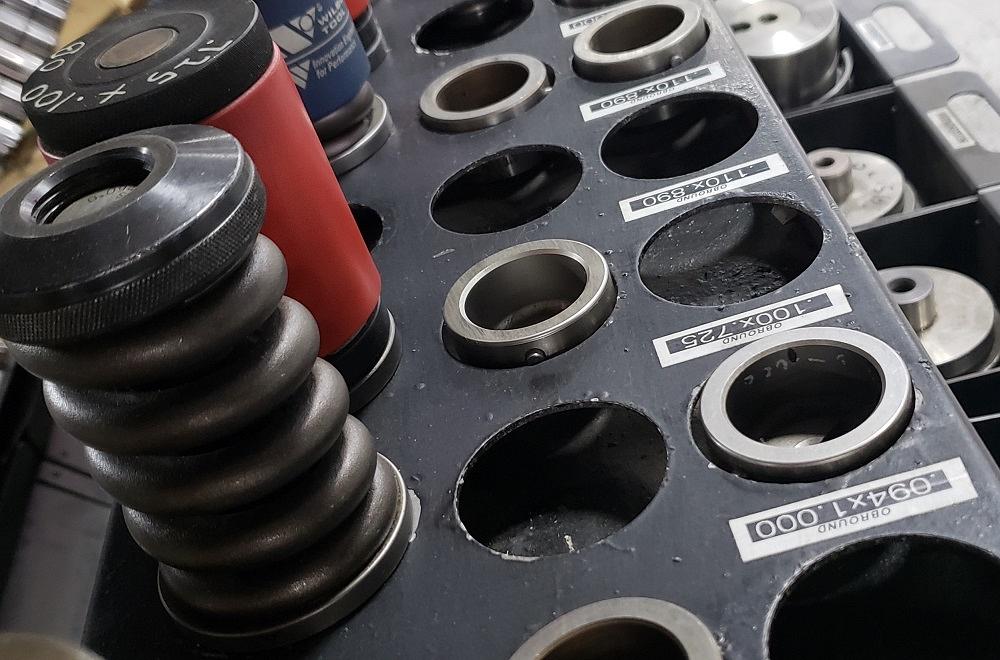
The Fine Line Of Effective 5s In Lean Manufacturing

The Visual Factory Modern Machine Shop Visual Factory Machine Shop Visual
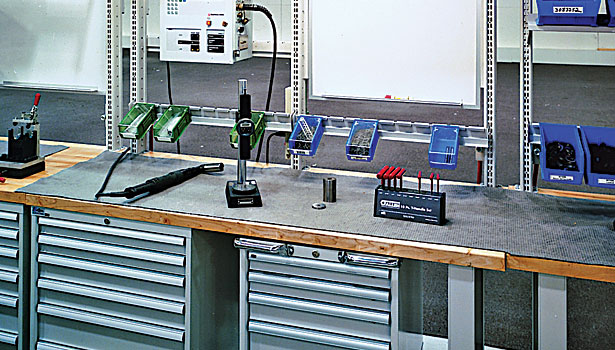
Implementing 5s In Assembly Plants Implementing 5s In Assembly Plants 12 03 01 Assembly Magazine

How The 5 S S Of Lean Manufacturing Helped Our Custom Cnc Machine Shop Fitzpatrick Manufacturing Co
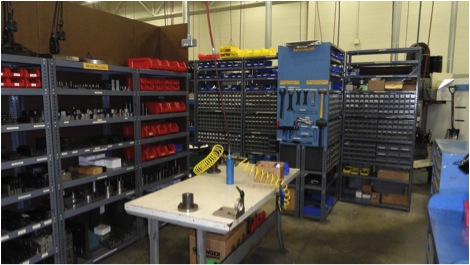
5s Visual Workplace Problems Identified Problems Solved Association For Manufacturing Excellence

5s Tpm Implementation At Leading Manufacturer Of Plastics Injection Moulding Machines Blow Moulding Machines In India Business Consultant Management Consulting Cbepl

Cnc Milling 5s Chautauqua Machine Specialties

Pdf Implementation Of 5s Methodology In A Metalworking Company

Here S How To Optimize And Automate Your Equipment With 5s

5s Workplace Organization Images Google Search Lean Manufacturing Industrial Flooring Kaizen
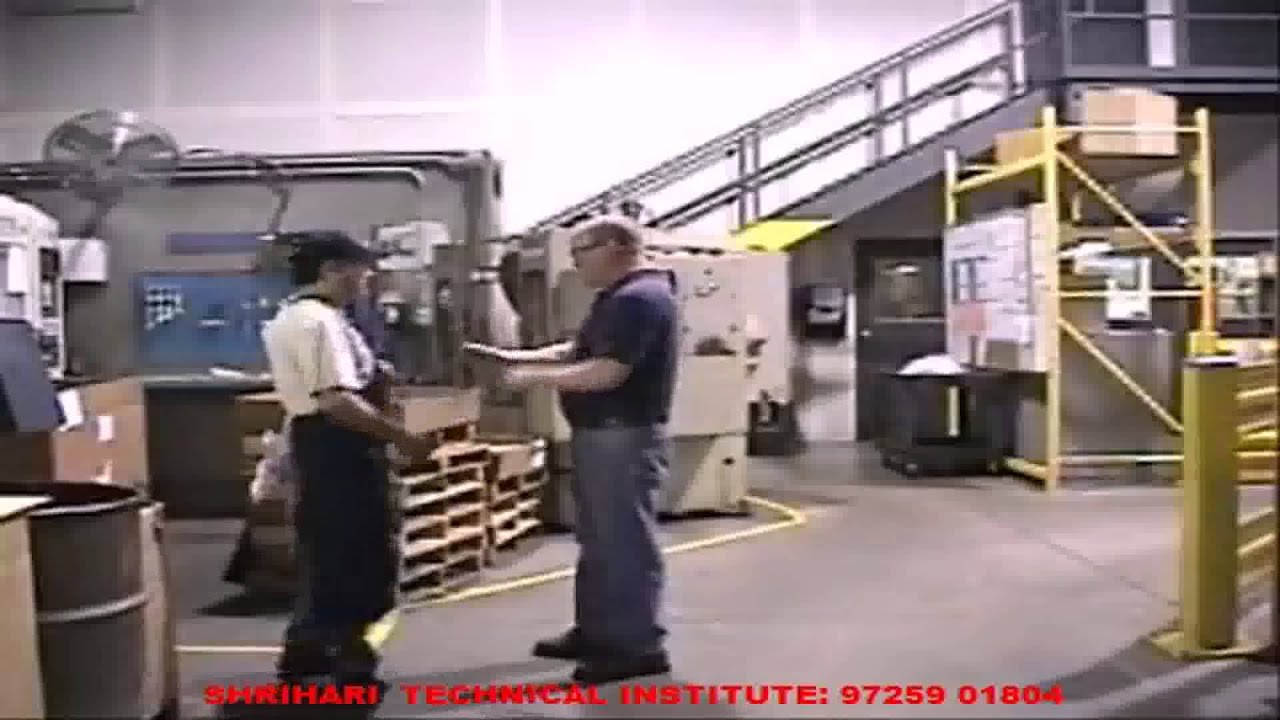
5s Machine Shop Training Youtube

Ai Powered 5s Board

Lean In To 5s 19 11 15 Quality Magazine

5s Posters Creative Safety Supply
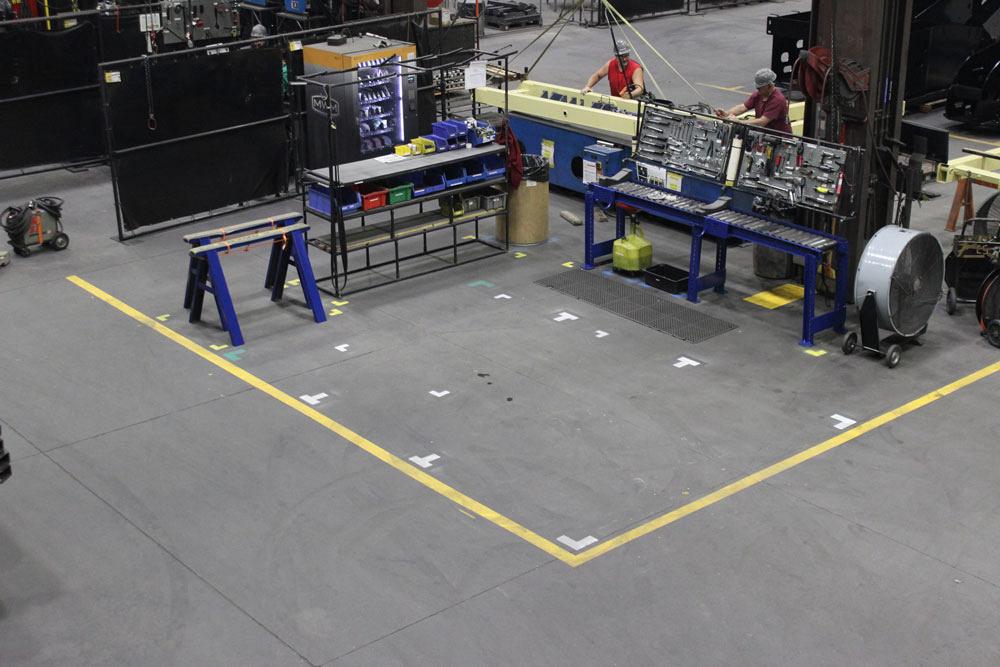
Fabricator Tackles The Focus And Flow Of Continuous Improvement

Our Company Jd Machine

5s Lean Manufacturing And Six Sigma Definitions
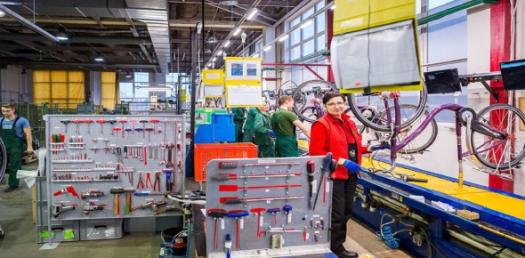
5s Visual Workplace Test Your Knowledge Trivia Quiz Proprofs Quiz
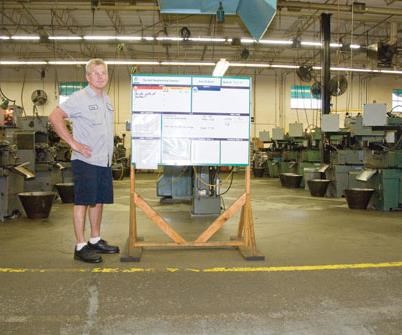
From Job Shop Chaos To Lean Order Modern Machine Shop
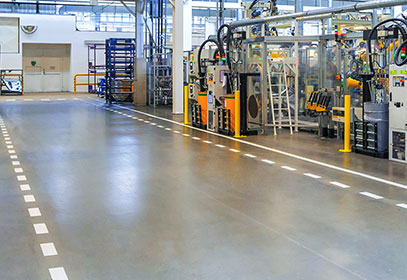
Floor Marking For 5s Creative Safety Supply

Superior Machining Fabrication On Jobshop Com
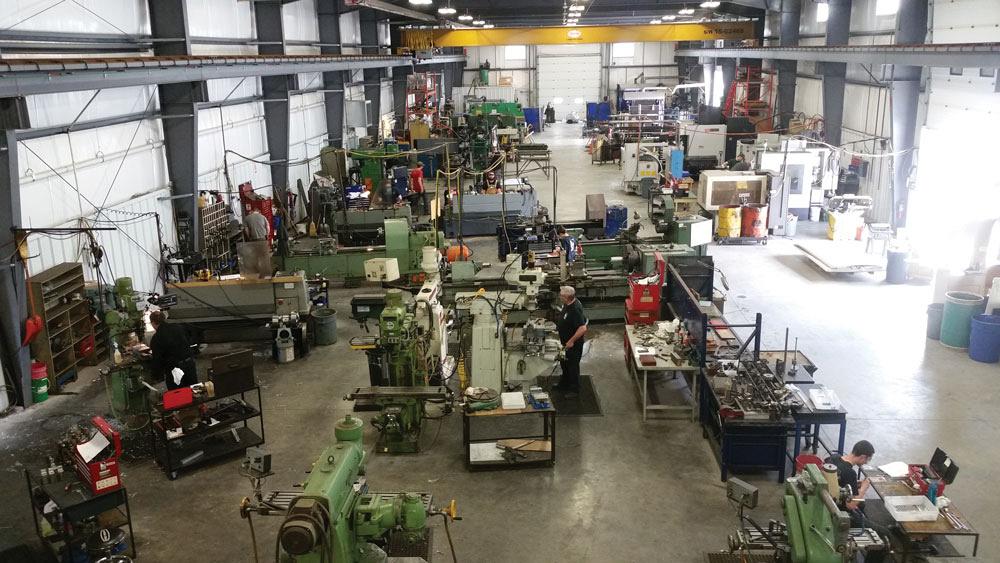
What Keeps You Up At Night

5s In The Laboratory What Why How

5s Organize For Productivity Lean Manufacturing Part 2 Cnccookbook Be A Better Cnc Er
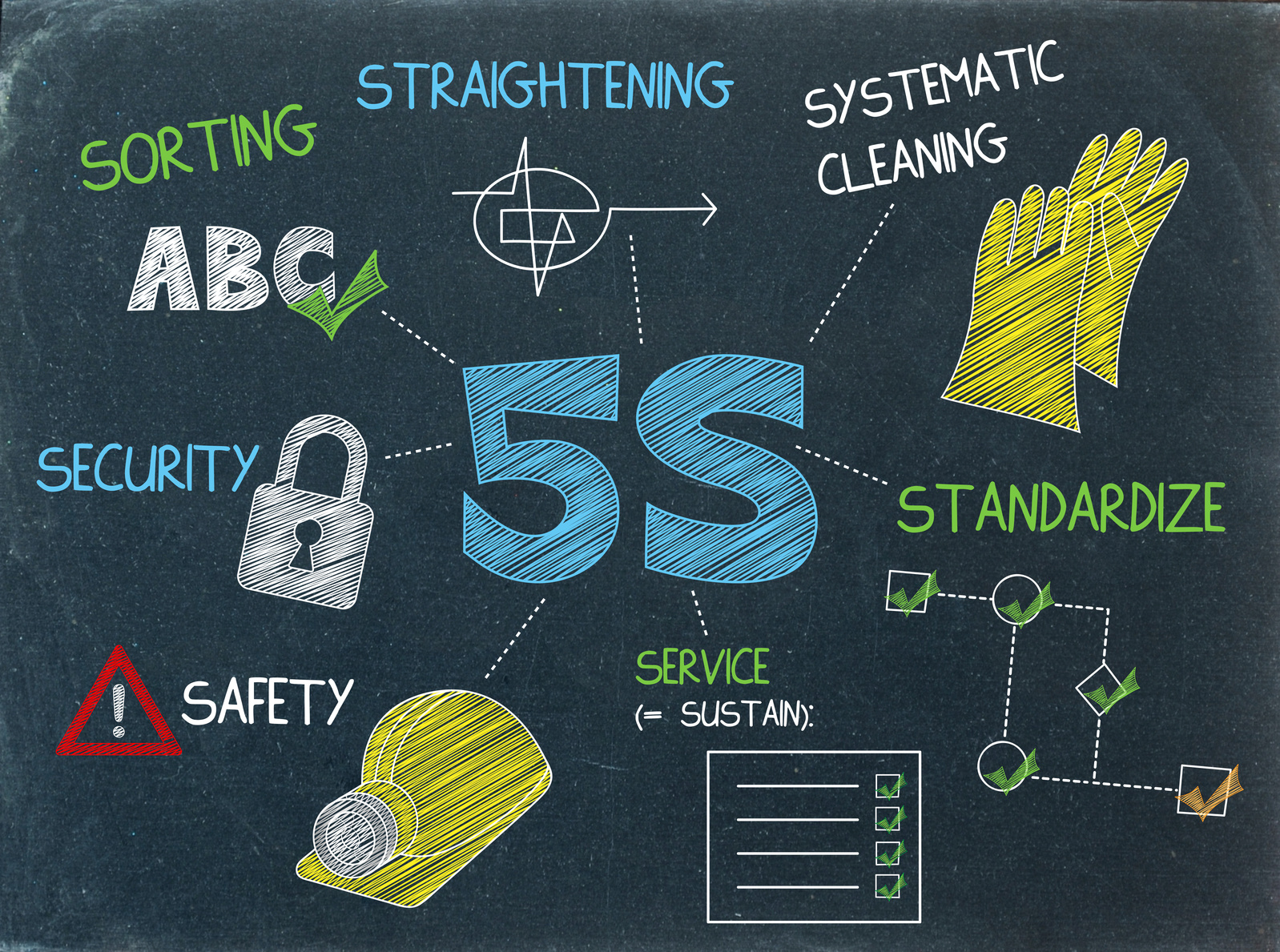
Implementing 5s In Machine Shops To Optimize Productivity Reduce Waste
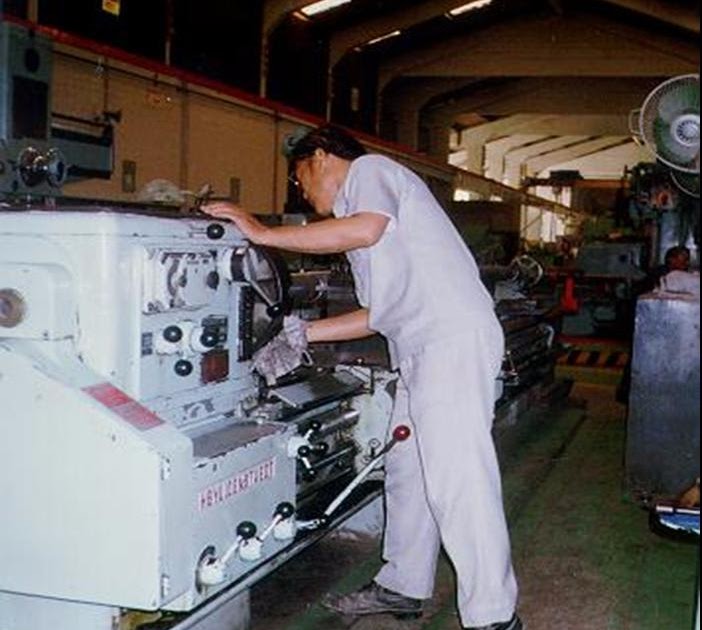
My 5s Corner How To Carry Out Seiso For Equipment
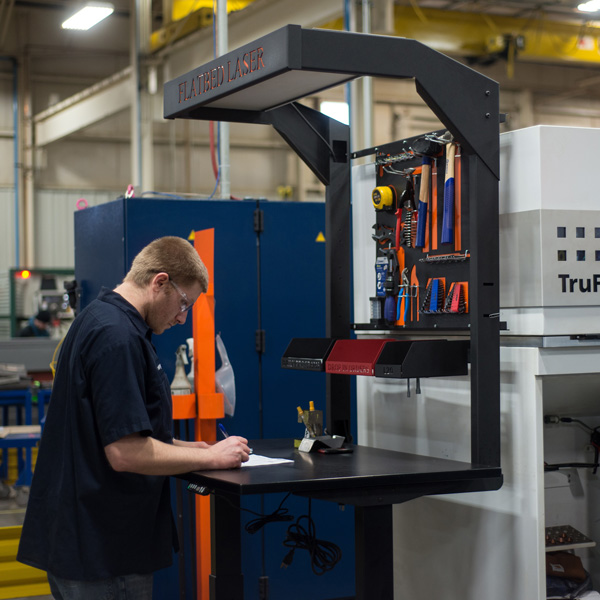
Sit Stand Workstation With 5s Tower Dectron Usa
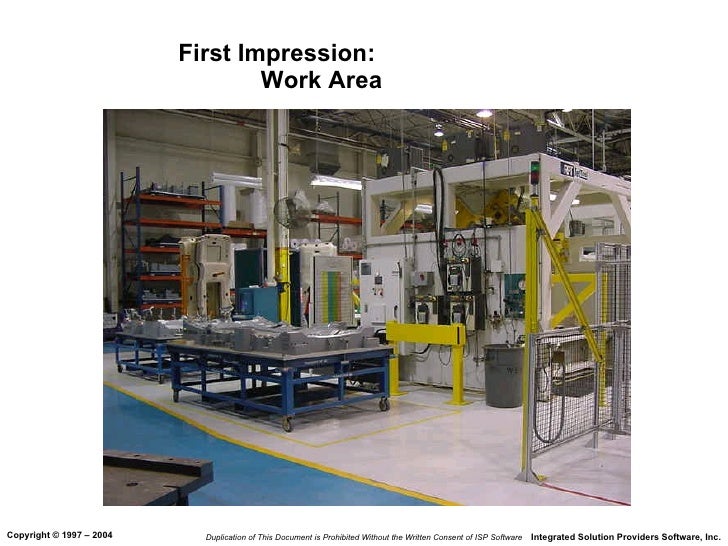
5s Workshop Visual Management Krishna Heda

5s In A Box Modern Machine Shop

5s Safetyculture

Lean 5s Seiso Sweep Shine Clean And Check

Why Safety Is Vital In Each 5s Step Wiley Metal

3 Top Ways A 5s Event Brought Order To Our Metal Fabrication Shop Wiley Metal
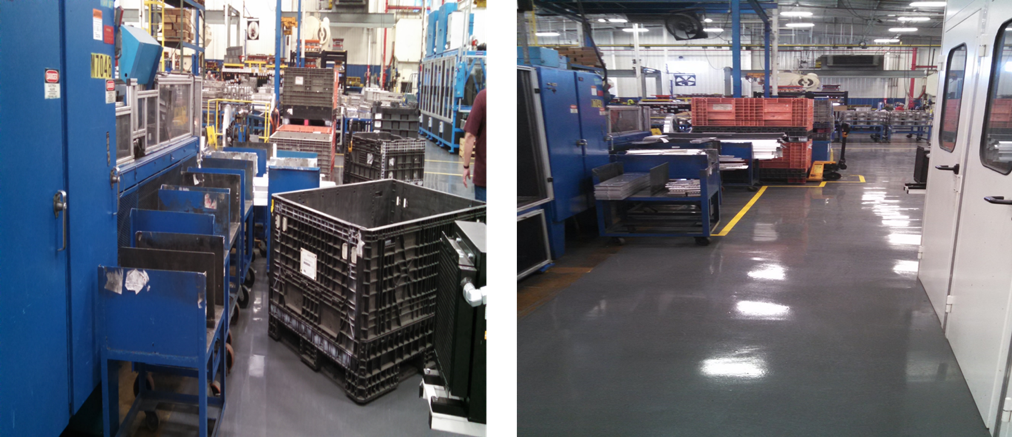
5s Workplace Organization Ut Center For Industrial Services
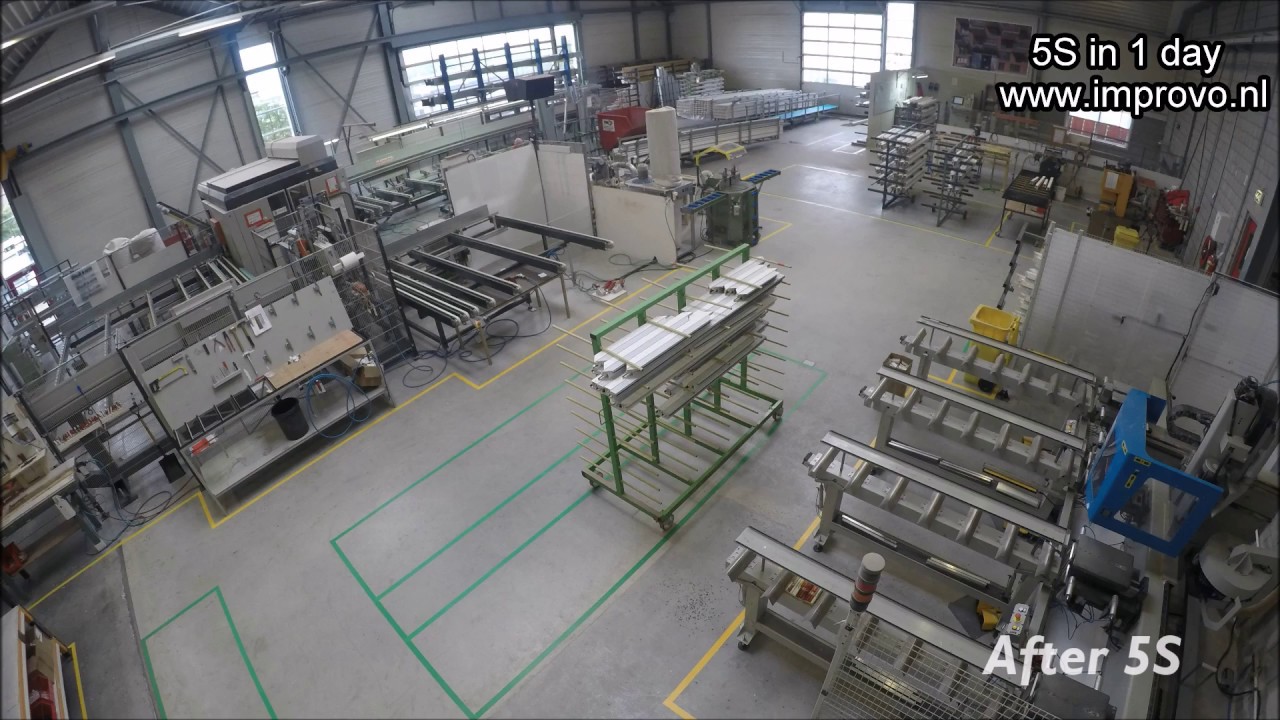
Factory Makeover 5s In 1 Day By Improvo Continuous Improvement Youtube

5s Organize For Productivity Lean Manufacturing Part 2 Cnccookbook Be A Better Cnc Er

5s Tools And Visual Management Tulip
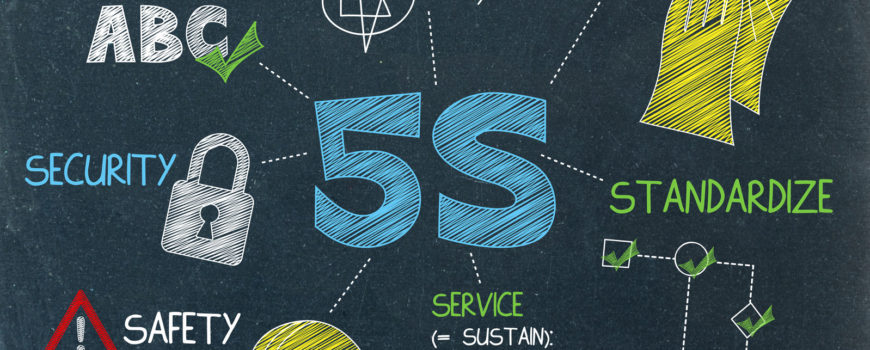
Implementing 5s In Machine Shops To Optimize Productivity Reduce Waste

5s Certification

5s Workplace Management Training In Ahmedabad Co Creative Solutions Id

How The 5 S S Of Lean Manufacturing Helped Our Custom Cnc Machine Shop Fitzpatrick Manufacturing Co
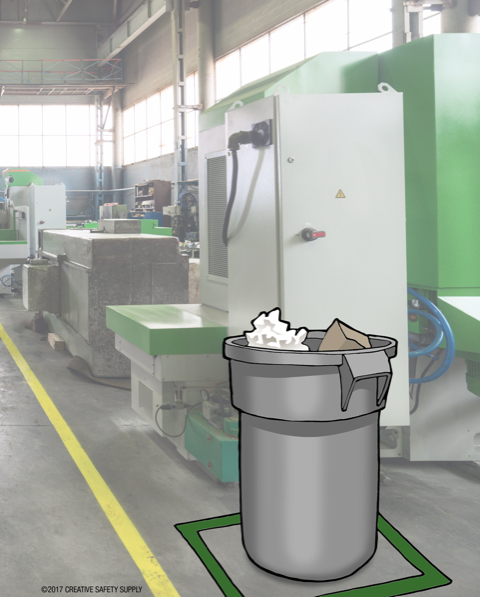
Floor Marking Is A Necessary Measure In The 5s And Lean Manufacturing Philosophies

Practical Machinist Largest Manufacturing Technology Forum On The Web

5s Machine Shop Training Youtube
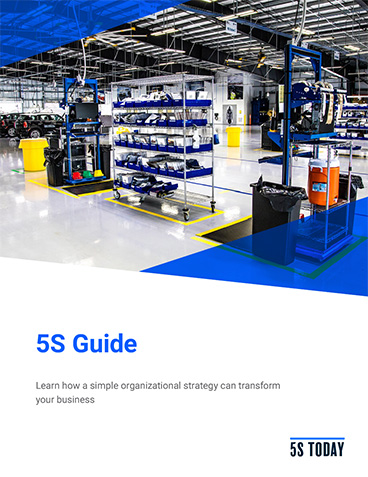
What Is 5s 5s System Is Explained Including Tips On Getting A 5s Program Started

Ningbo Jieda Mold Workshop S Improvement In 5s Jieda Molding Machine
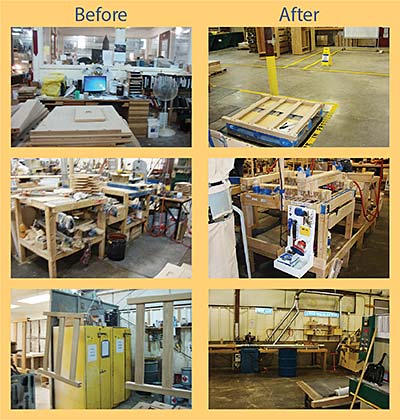
Mount Pleasant Shines After 5s Event
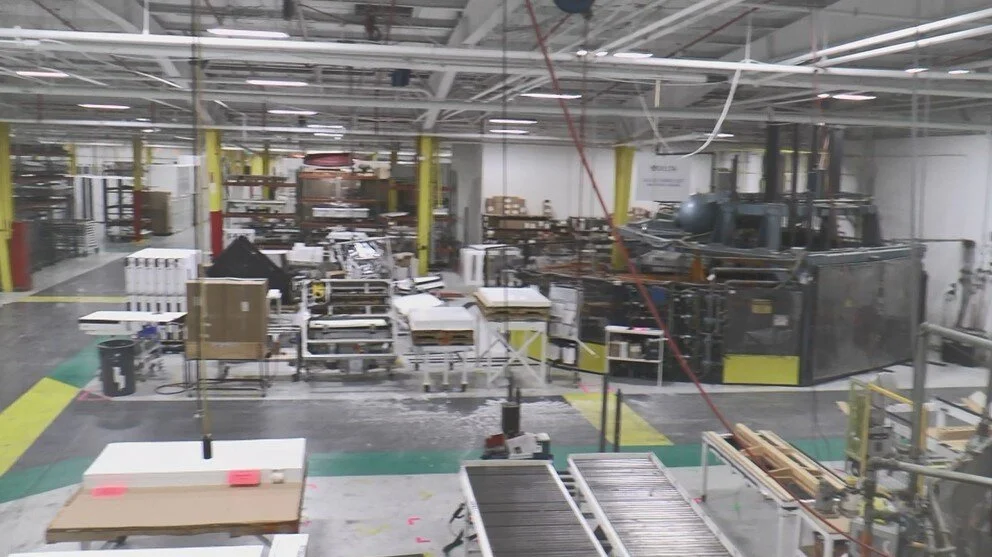
What Most Business Leaders Do Not Recognize About The Value Of 5s Valueflo Consulting
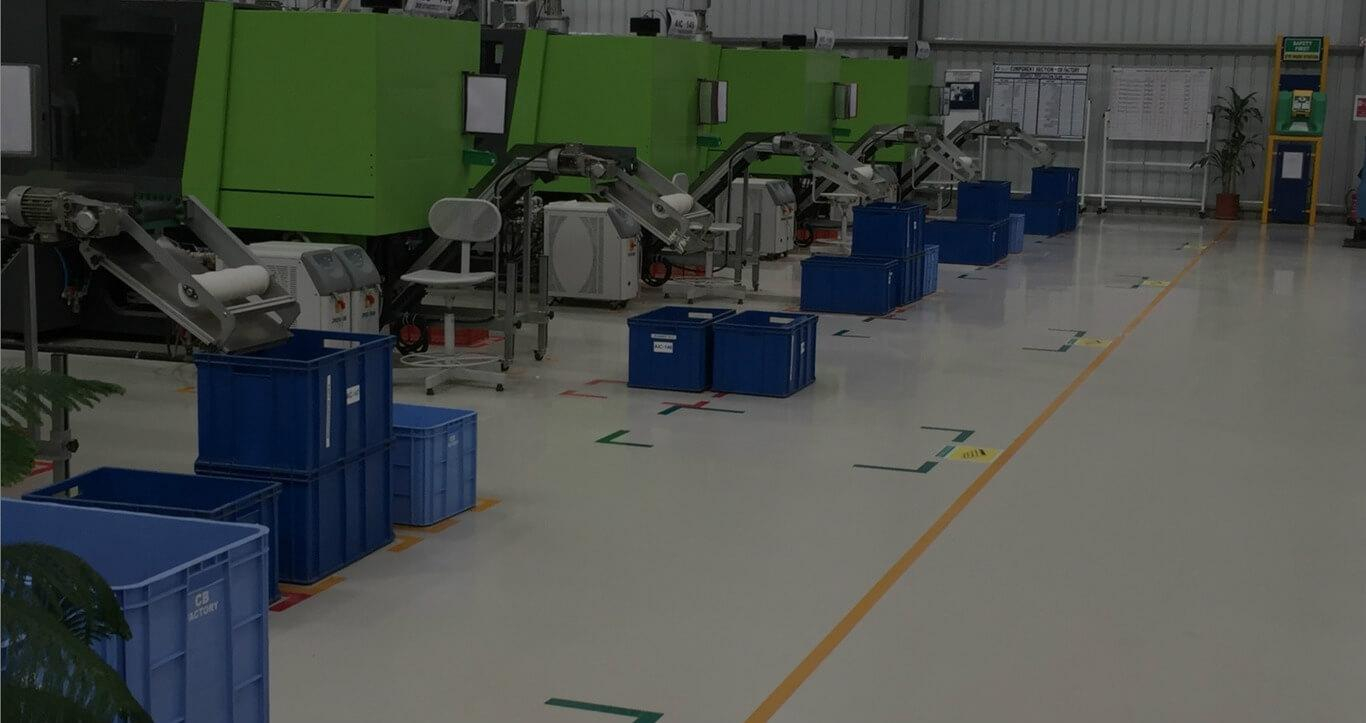
Method 5s Explanations And Example Of The 5s Lean Sesa Systems

Success With The 5s Method Hoffmann Group
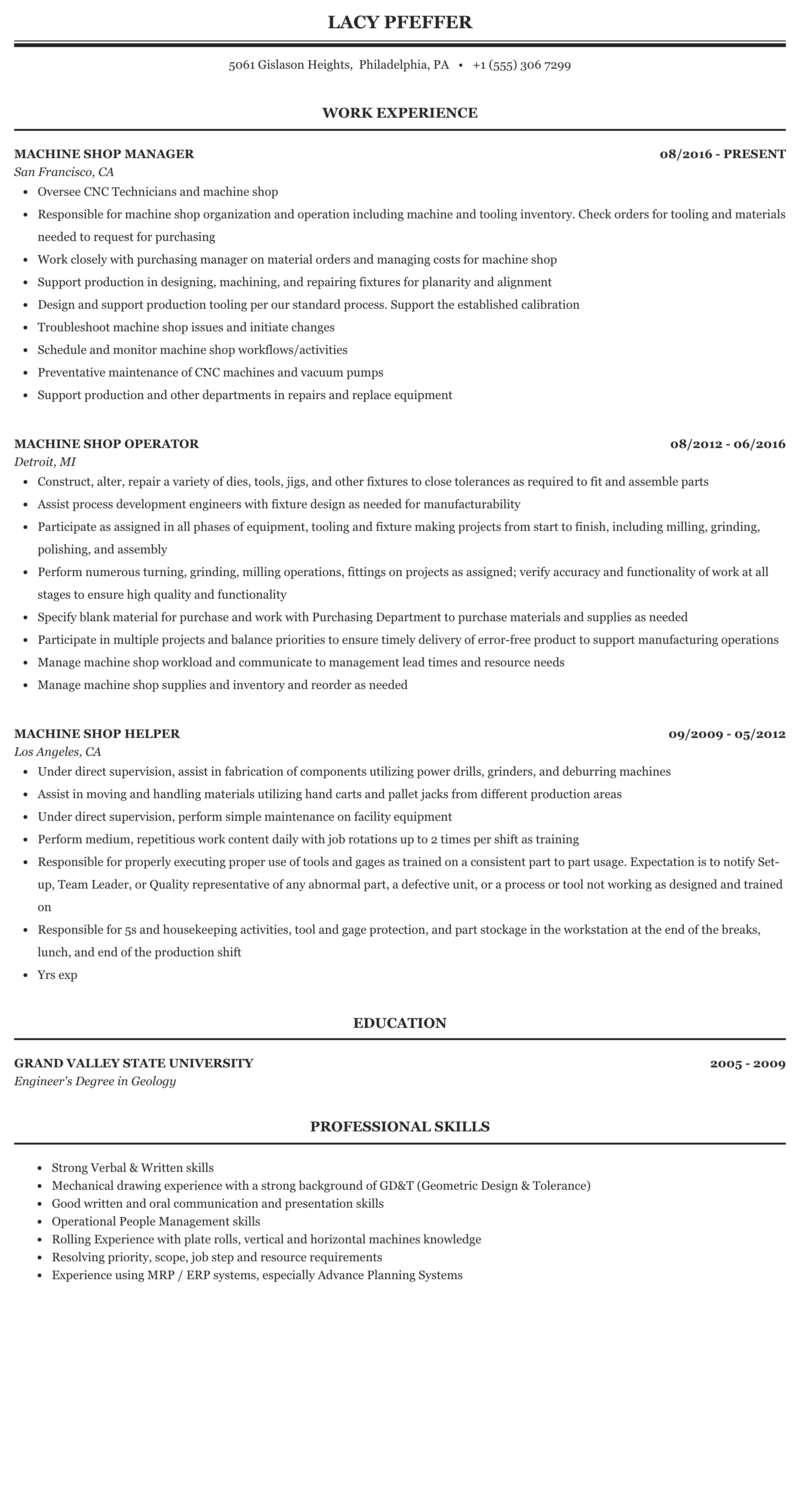
Machine Shop Resume Sample Mintresume
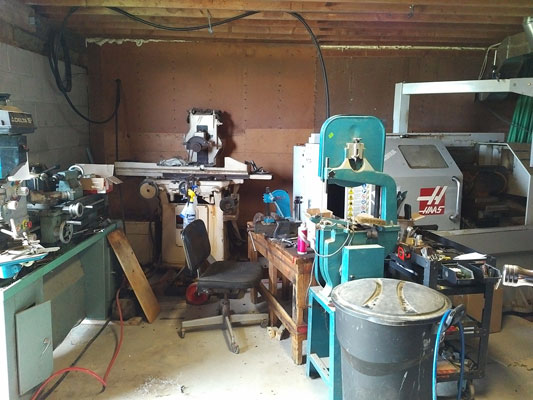
Keep Machine Shops And People Cool Clean And Safe Dummies
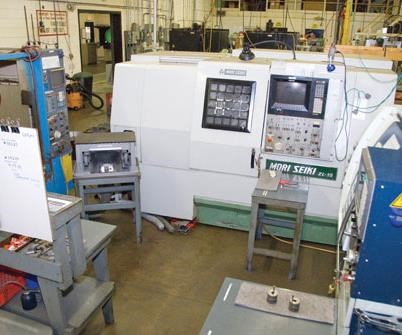
From Job Shop Chaos To Lean Order Modern Machine Shop

5s Machine Shop Training Youtube

Numericraft An As9100 Iso 9001 Precision Cnc Machine Shop

Seiso Means Shine In 5s Lean Methodology Click Here
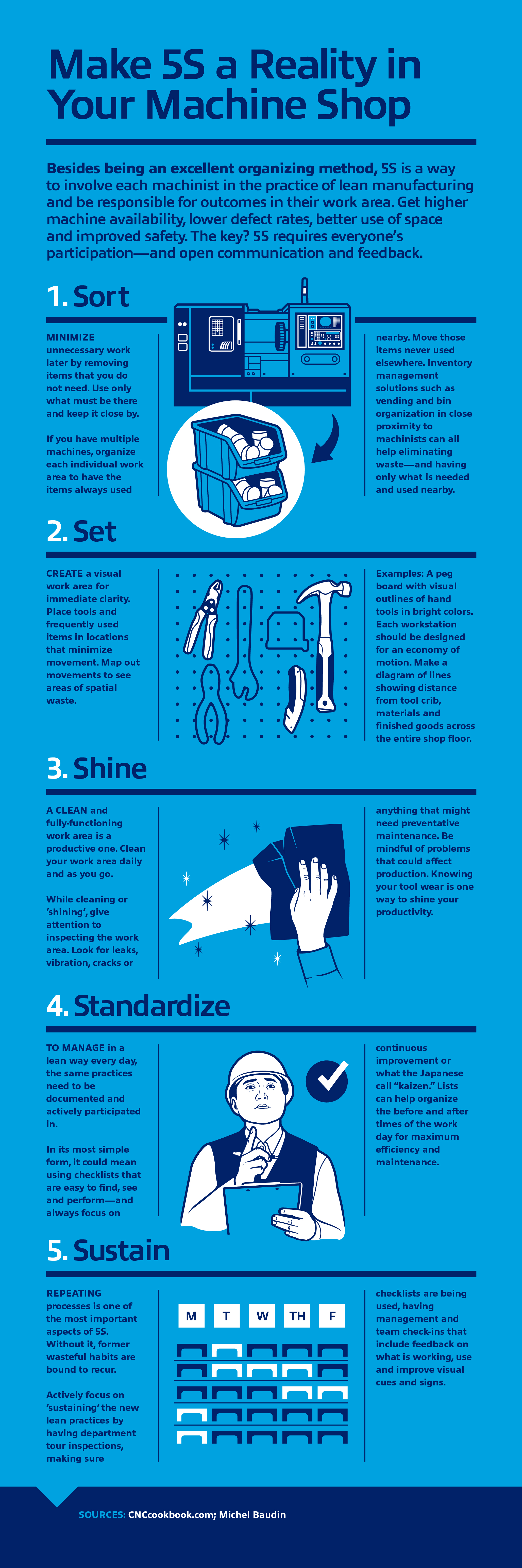
Infographic Make 5s A Reality In Your Machine Shop Better Mro

Beginner S Guide To Cnc Machine Setup 19 Cnc Setup

Poster De 5s Clasificar Espanol Spanish Poster Enna Com