Maintenance Workshop 5s
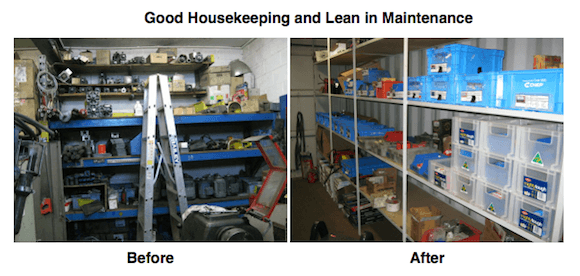
Maintenance As An Essential Part Of Lean
Www Ijstr Org Final Print Feb15 Implementation Of 5s Quality Tool In Manufacturing Company A Case Study Pdf
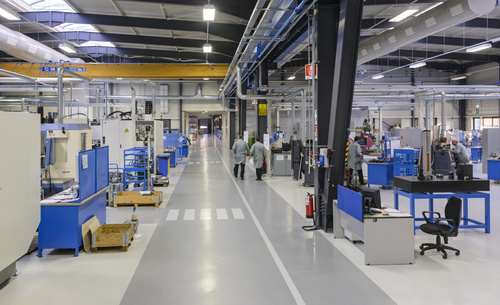
5s Method Housekeeping Factory Systems

Here S How To Optimize And Automate Your Equipment With 5s
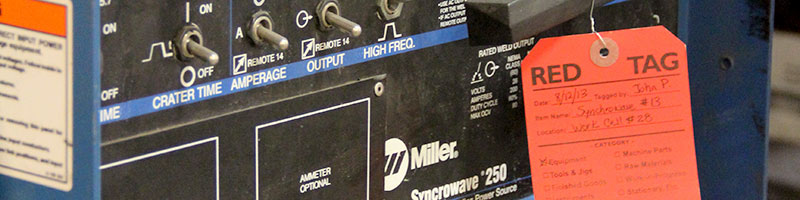
What Is 5s 5s System Is Explained Including Tips On Getting A 5s Program Started

5s Tpm Bundle Reliability Engineering Powerpoint Powerpoint Templates
DEVELOP a Lean Maintenance Methodology What applies to operations applies to maintenance Methodologies, such as 5S, singleminute exchange of dies (SMED), standard work and kanban, all can be exemplified in the maintenance department For example, with 5S, everything should have a designated place and be in its place.
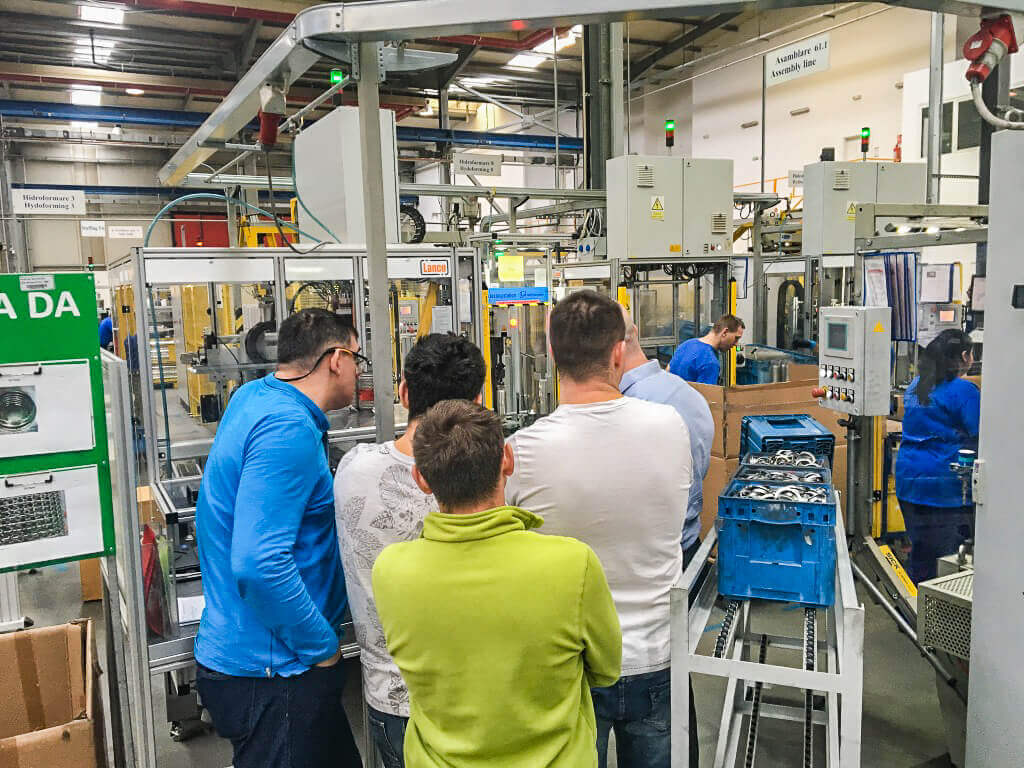
Maintenance workshop 5s. Maintenance costs or equipment rental (Crespo 15) The present research starts from the hypothesis that implementing 5S in the maintenance workshop of a road construction company will improve its efficiency, the availability of equipment and the workplace environment So, a pilot implementation was. To start the 5S StepbyStep Implementation, each phase must be thoroughly analysed and addressed using the PDCA Cycle and 5W2H approach as follows Provide training and education for everyone Form 5S Council Setup 5S Zones Determine 5S objectives, goals and implementation phases Plan 5S action plan and 5S Launch DO PLAN Set in Order. Setting up a 5S program in a maintenance shop is harder than training a cat to use the toilet It can be done, but it could become a very long and tedious process 5S in a maintenance shop has challenges that 5S on the production floor doesn't In a production environment, even a poorly developed process has understandable steps.
Once an organization determines the 5S strategies are a good fit for the company, they need to start planning out how to implement 5S Proper implementation will require physical changes to the facility, as well as training employees and other parties to operate in accordance with the 5S methodology It can take quite some time before 5S is fully implemented, but there will be significant. 5S Audit Form (3032 KB) 5S Launch Guide ( KB) 5S Maintenance Chart (6627 KB) 5S Materials Checklist ( KB) 5S PowerPoint Training Presentation (7 MB) 5S Project Charter (12 KB) 5S Weekly Team Meeting (1431 KB). Initial Control 5S Pillars Autonomous Maintenance – Jishu Hozen Planned Maintenance Quality Maintenance – Hinshitsu Hozen Focused Improvement – Kobetsu Kaizen Early Equipment Management Education & Training Safety, Hygiene & Environment Office TPM.
To be successful in implementing 5S (Sort, Set, Shine, Standardize, Sustain), audits must be conducted and four simple rules followed Everything HAS a place and everything IN its place Nothing on the Floor, except Legs, Wheels, or Pallets Clean to Inspect, Inspect to Detect, Detect to Correct, Correct to Perfect When in doubt, throw it out. 5S begins with the Sort step Sort is the cornerstone of 5S and will help get rid of problems such as • Tools and materials impeding workflow • Wasted time looking for parts, tools, and products • Stockpiling unnecessary and expensive inventory • Safety hazards resulting from clutter. How can people be motivated to do it?.
I am interested in "5S" (seiri, seiso, seiton, seiketsu, shitsuke) or CANDO as known in the USA What experience do you have?. Training he has conducted are Quality Control Circle Facilitator, Suggestion System, ISO 9000, ISO , 5S, Total Productive Maintenance, Autonomous Maintenance, On the Job Training (OJT), Supervisory Management , Statistical Process Control, 7 QC Tools & Management Tools, Just In Time, Train The Trainer, Exploratory Survey. Autonomous Maintenance Training Workshop A unique 2 days’ Autonomous Maintenance Workshop how to improve your OEE while reducing your maintenance cost!.
The overall 5S Level of Achievement is the lowest level attained for any of the S's 5S is only as good as its weakest link If a work area has not addressed Standardizing and Sustaining, no matter how high the level achieved for the other S's, the area will eventually revert to a non5S state. The other options to include with 5S are Safety, Security and Spirit Safety Safety is often said that it is implied within 5S that everything should be done with safety as the number one priority, but to ensure that is the case, Safety is added as an additional S It is particularly prominent in manufacturing, warehouses, heavy equipment. Skip to content Call Us At (8) ;.
A 5S basics, interesting, fun 1day Introduce to 5S Workplace Management for Shopfloor People, Supervision and Managers You get 5S training workshop material containing a 5S PPT PowerPoint Presentation of foundational 5S knowledge, and a 5S game people play that puts them into a 5S Simulation where they continually improve and learn the value of 5S. 5S involves assessing everything present in a space, removing what's unnecessary, organizing things logically, performing housekeeping tasks, and keeping this cycle going Organize, clean, repeat Let's take a closer look at each of the parts of 5S. The "5s" are the core elements of total productive maintenance, which serve as the foundation for TPM When implemented correctly, the 5s help create a clean, safe, efficient, and organized workplace that boosts equipment effectiveness, improves efficiency, and reduces waste The 5s of total productive maintenance are as follows.
5S is sometimes called the five pillars because just like the physical pillars that hold up a structure, 5S has five elements that support the effectiveness of the system And just like the pillars of a building, if one was to weaken or fail, the entire structure would fall The five steps/pillars of 5S are 1 Sort 2 Set in Order 3 Shine. Autonomous Maintenance Gives Operators Freedom and Responsibility Autonomous maintenance (AM) is performed by the operators and not by dedicated maintenance techniciansIt is a crucial component of the Total Productive Maintenance (TPM)The core idea of autonomous maintenance is to provide the operators with more responsibility and allow them to carry out preventive maintenance tasks. The 5S methodology was born at Toyota in the 60s under an industrial environment to achieve better organized, tidier, and cleaner workplaces to increase productivity and to obtain a better working environment The 5S methodology has been widely spread, and many companies and organizations are implementing it worldwide Although it is conceptually simple and does not require a complex training.
Autonomous Maintenance Training Workshop A unique 2 days’ Autonomous Maintenance Workshop how to improve your OEE while reducing your maintenance cost!. The Shine stage of 5S focuses on cleaning up the work area, which means sweeping, mopping, dusting, wiping down surfaces, putting tools and materials away, etc In addition to basic cleaning, Shine also involves performing regular maintenance on equipment and machinery. 5S methodology has expanded from manufacturing and is now being applied to a wide variety of industries including health care, education, and government Visual management and 5S can be particularly beneficial in health care because a frantic search for supplies to treat an introuble patient (a chronic problem in health care) can have dire.
This study focuses on the application of 5S in welding workshop, to simplify wasteful activities Industrial Maintenance & Plant Operation, 69 (1 0), 54 2 Michalska J and Szewiecz ek D 07. The Shine stage of 5S focuses on cleaning up the work area, which means sweeping, mopping, dusting, wiping down surfaces, putting tools and materials away, etc In addition to basic cleaning, Shine also involves performing regular maintenance on equipment and machinery. What are the Five S's (5S) of Lean Quality Glossary Definition Five S’s (5S) 5S is defined as a methodology that results in a workplace that is clean, uncluttered, safe, and well organized to help reduce waste and optimize productivity.
Maintenance costs or equipment rental (Crespo 15) The present research starts from the hypothesis that implementing 5S in the maintenance workshop of a road construction company will improve its efficiency, the availability of equipment and the workplace environment So, a pilot implementation was. Used it to tidy up the maintenance workshop, and resulted in improved morale, and fewer 'repeat failures' as the guys worked more 'tidily' a sort of virtuous circle. Housekeeping is housekeeping, not 5S 5S is a visual system and a system for engaging employees 5S must be a team effort and the results must enable anyone to "tell at a glance" what is right and what is out of place It also must make doing the work easier Implementing 5S occurs in two phases initial implementation and later refinement.
5S is a method to improve and sustain workplace organisation 5S represents 5 disciplines for maintaining a visual workplace (visual controls and information systems)These are foundational to continual improvement and a manufacturing strategy based on “ Lean Manufacturing ” (waste removing) concepts 5S help reduces clutter, reduces the time it takes to look for tools and equipment. 5S is amongst the first and fundamental steps implemented by an enterprise towards the path of implementing Total Quality Management and continuous improvement at the operation level 5S is a process designed to organize the workplace, keep it clean,. A showcase presented by SIRF Roundtables VICTAS Showcasing 5S in Maintenance and Workshops in the Northern Vic region Schneider Electric Benalla & Thales Benalla Come join your peers to visit two excellent sites and gain valuable insights in, Securing & sustaining workshop 5S Parts and equipment storage New workshops Optimising layout, storage & workflow Attendance is free for people from.
The "5s" are the core elements of total productive maintenance, which serve as the foundation for TPM When implemented correctly, the 5s help create a clean, safe, efficient, and organized workplace that boosts equipment effectiveness, improves efficiency, and reduces waste The 5s of total productive maintenance are as follows. The three steps in this process are assigning 5S (Sort, Set in Order, Shine) job responsibilities, integrating 5S duties into regular work duties, and checking on the maintenance of 5S Some of the tools used in standardizing the 5S procedures are job cycle charts, visual cues (eg, signs, placards, display scoreboards), scheduling of "five. 5S is one of the most widely adopted techniques from the lean manufacturing toolbox Along with Standard Work and Total Productive Maintenance, 5S is considered a "foundational" lean concept, as it establishes the operational stability required for making and sustaining continuous improvements The primary objective of 5S is to create a clean, orderly environment an environment where there is a place for everything and everything is in its place.
The overall 5S Level of Achievement is the lowest level attained for any of the S's 5S is only as good as its weakest link If a work area has not addressed Standardizing and Sustaining, no matter how high the level achieved for the other S's, the area will eventually revert to a non5S state. This is sometimes called 5S, 6S, lean 6S, 6S safety, or lean 6S safety In this article, we’ll learn more about 5S and/or 6S and how you can use it to create a more organized, efficient, productive, and safe workplace To learn even more, check out our series of 5S online training courses and lean manufacturing training courses. Nufarm have enthusiastically been heading down the path of 5s in a maintenance workshop, they are kindly hosting this workshop and will share on their experience and insights This will be an opportunity to hear their journey of 5S in a maintenance workshop while also creating an opportunity to share and learn from others attending.
The 5S methodology is a simple yet effective technique to improve the way your office functions Let’s explore how implementing this methodology can establish discipline, order, and efficiency in your workplace History of 5S 5S is believed to have started as early as the 16th century with the Venetian shipbuilders in Venice, Italy. > Total Productive Maintenance and 5S are two methodologies that seem somewhat distant, but the reality is that applying them effectively at the same time can lead to a great synergetic effect that boosts the performance of your company even more In the end, they both strive to achieve the same goal in different way,. 5S Lean Workshop Management Training 2 Day Training course by Striving Minds Consulting Introduction to 5S 5S is workplace management where the work area and workplace are organised and ritualised to minimise the loss of time and the use of movement Originally part of Lean manufacturing.
Used it to tidy up the maintenance workshop, and resulted in improved morale, and fewer 'repeat failures' as the guys worked more 'tidily' a sort of virtuous circle We've neglected it recently, and moved to a new workshop time to do it again. Nufarm have enthusiastically been heading down the path of 5s in a maintenance workshop, they are kindly hosting this workshop and will share on their experience and insights This will be an opportunity to hear their journey of 5S in a maintenance workshop while also creating an opportunity to share and learn from others attending. A 5S can be applied to any work environment It could be a supply/store in a hospital, a repair truck for a telecom company, a CSR desk/work area in a call center, the baggage claim area of an airline or a laptop computer.
Training content 1 Presentation of the 5S approach 2 Description of the 5 steps 3 Visual management 4 Workshop animation description 5 Key Success Factors to maintain 5S results and to set up continuous improvement 6 5S workshop on pilot project on a working area of your choice 7 Action plan with remaining tasks to be performed on. This powerful course teaches delegates the concepts and implementation skills necessary to implement and manage Autonomous Maintenance, one of the key pillars in Total Productive Maintenance. 5S is a formulaic method you can use to straighten and organize a work area Using 5S reduces waste (a fundamental goal in lean manufacturing), improves safety (see our article on Lean 6S Safety ), and otherwise improves your production process and work environment 5S is called 5S because their are 5 steps and each step begins with the letter “S” (and/or the sound “s”).
Course5Sdocx 18 June 10 Page 1 of 3 Introduction to 5S Training Workshop Welcome to the oneday 5S training course by Lifetime Reliability Solutions Introduction to 5S 5S is workplace management where the work area and workplace are organised and ritualised to minimise the loss of time and the use of movement. Training participants are typically tasked to complete both individual and team activities covering each of the 5 principles 5S training is best conducted in the individual or team’s place of work as this maximizes efficiency by going through training while actually practicing 5S in your workspace. As 5S This section will detail how a 5S initiative that focuses on a plant’s Preventive Maintenance (PM) program can immediately unlock resources within the maintenance department and make the PM process significantly more effective and efficient Part 2 will look at the Deadly Wastes (Muda) of manufacturing and how elimination of these.
5S is amongst the first and fundamental steps implemented by an enterprise towards the path of implementing Total Quality Management and continuous improvement at the operation level 5S is a process designed to organize the workplace, keep it clean, maintain effective and standard conditions. The workshop will cover also the implementation structure and resources needed, including the three types of documents of 5S, the evaluation and audit criteria, and the key objectives for each step This is an interactive session with simulations to allow participants to immediately bring this technique to their workplace. › 5S Red Packs 5S Red Packs 5S Red s are used to keep the process of change going throughout the 5S workshop while remaining organized in the process 5S Red s are used for visual management of a workspace, clearly marking items that need to be moved creating workplace organization.
Make your workshop look professional Tool Board Tool Shadows. The 5S methodology comes from Japan, and each "s" stands for the Japanese words "seiri," "seiton," "seiso," "seiketsu" and "shitsuke" Roughly translated into English "s" words, they represent "sort," "set in order," "shine," "standardize" and "sustain" The premise of 5S is to help organize and improve the work conditions of a workplace. Years ago, in rolling out a TPM program, one of the first things we tackled was 5S in the maintenance workshop I remember as a young reliability manager, overhearing a casual conversation between my manager and our tool maker, while standing next to our lathe My manager said something along lines ofI know as a tool maker you have such.
If 5S is implemented in the workshop of a road construction company, will improve its efficiency and availability of heavy machinery and occupational safety indicators Measure the current situation of the workshop under study, using indicators of maintenance of road equipment and occupational safety Know the effects of 5S implementation. 5S GOOD HOUSEKEEPING TECHNIQUES 1 1 What is 5S all about?. 5S & Lean Organization and Maintenance Supplies We have what you need for Lean, 5S and Visual Workplace Solutions that make your work easier and safer!.
TOYOTA 5S Training Maintenance Introduction to the 5 Pillars of 5S • SIFT (Seiri) Organization SORT (Seiton) Orderliness SWEEP & WASH (Seiso) Cleanliness SPIC & SPAN (Seiketsu) Standardized Way of maintaining Sift, Sort, Sweep and Wash • SUSTAIN (Shitsuke) Discipline. This powerful course teaches delegates the concepts and implementation skills necessary to implement and manage Autonomous Maintenance, one of the key pillars in Total Productive Maintenance. The "5s" are the core elements of total productive maintenance, which serve as the foundation for TPM When implemented correctly, the 5s help create a clean, safe, efficient, and organized workplace that boosts equipment effectiveness, improves efficiency, and reduces waste The 5s of total productive maintenance are as follows.
The 5S program sets the pace for the introduction of Total Productive Maintenance and must be fully mature before any attempts are made to implement other aspects of the system As a standalone component, 5S is very effective in improving the organizational metrics and has been shown to increase aspects such as productivity and quality. Training he has conducted are Quality Control Circle Facilitator, Suggestion System, ISO 9000, ISO , 5S, Total Productive Maintenance, Autonomous Maintenance, On the Job Training (OJT), Supervisory Management , Statistical Process Control, 7 QC Tools & Management Tools, Just In Time, Train The Trainer, Exploratory Survey. Training content 1 Presentation of the 5S approach 2 Description of the 5 steps 3 Visual management 4 Workshop animation description 5 Key Success Factors to maintain 5S results and to set up continuous improvement 6 5S workshop on pilot project on a working area of your choice 7 Action plan with remaining tasks to be performed on.
5S is sometimes called the five pillars because just like the physical pillars that hold up a structure, 5S has five elements that support the effectiveness of the system And just like the pillars of a building, if one was to weaken or fail, the entire structure would fall The five steps/pillars of 5S are 1 Sort 2 Set in Order 3 Shine.
Http Www Intracen Org Uploadedfiles Intracenorg Content Exporters Exporting Better Quality Management Assetpdf Bulletin eqm 5s Pdf

5s Methodology Wikipedia
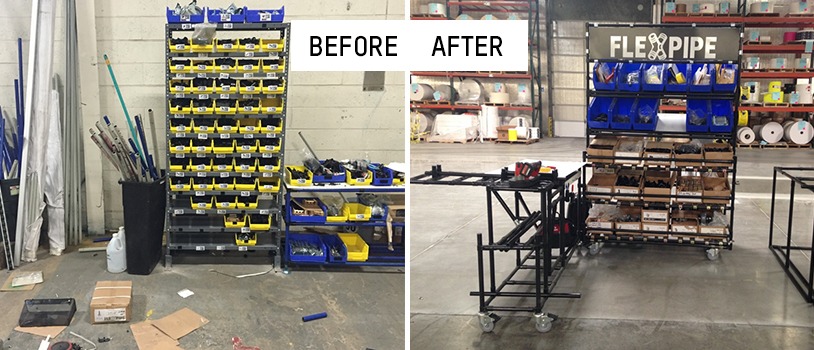
Why Your Workplace Should Include A Flexpipe Crib Flexpipe

The Essence Of 5s Cierpa Lean Software
Q Tbn And9gctnoy Wk6gvmgz1oc2hej1ddhirvt2bhendqhnywsmk8mbqg42o Usqp Cau

5s Operational Excellence Targus
Www Mdpi Com 71 1050 11 14 37 Pdf

5s Images Library See What 5s Looks Like In Action
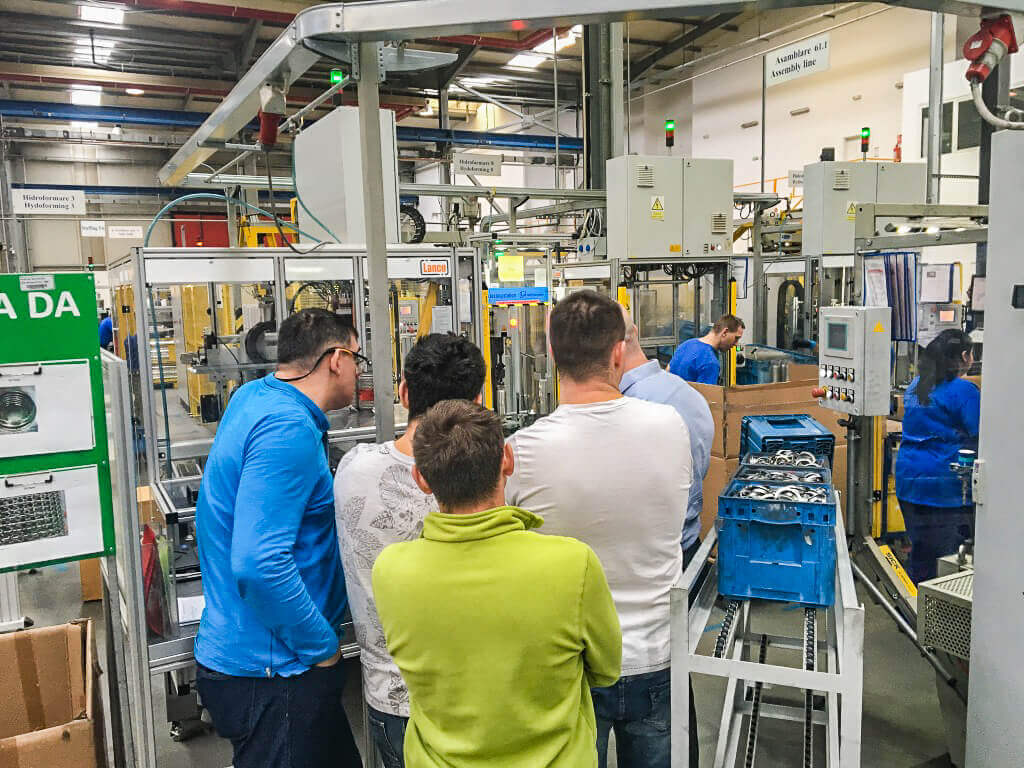
Tpm In Field Training

5s Visual Management Group

Formation Lean

How To Apply 5s Method To Improve Shop Efficiency 18 12 06 Snips

5s Tpm Implementation At Leading Manufacturer Of Plastics Injection Moulding Machines Blow Moulding Machines In India Business Consultant Management Consulting Cbepl

Before And After Professional Garage Organization Using The 5s Japanese Organization Method Converted Garage Garage Organization Garage Renovation
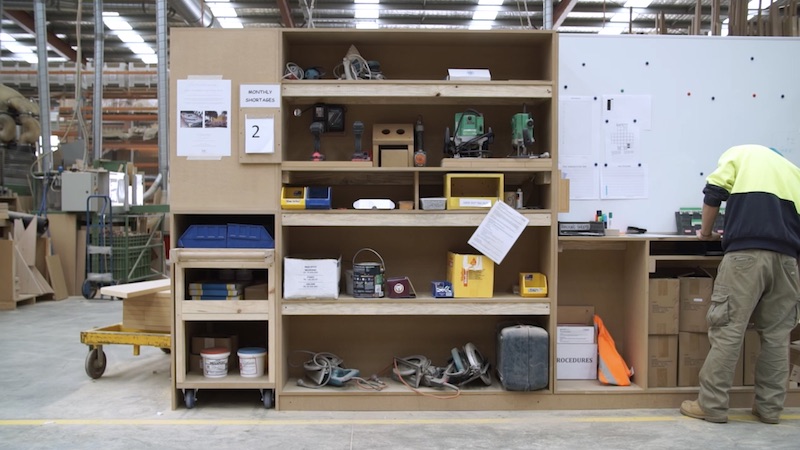
Is 5s Really Just A Waste Of Time Txm Lean Solutions

The 5s Of An Organized Metal Fabrication Shop Wiley Metal
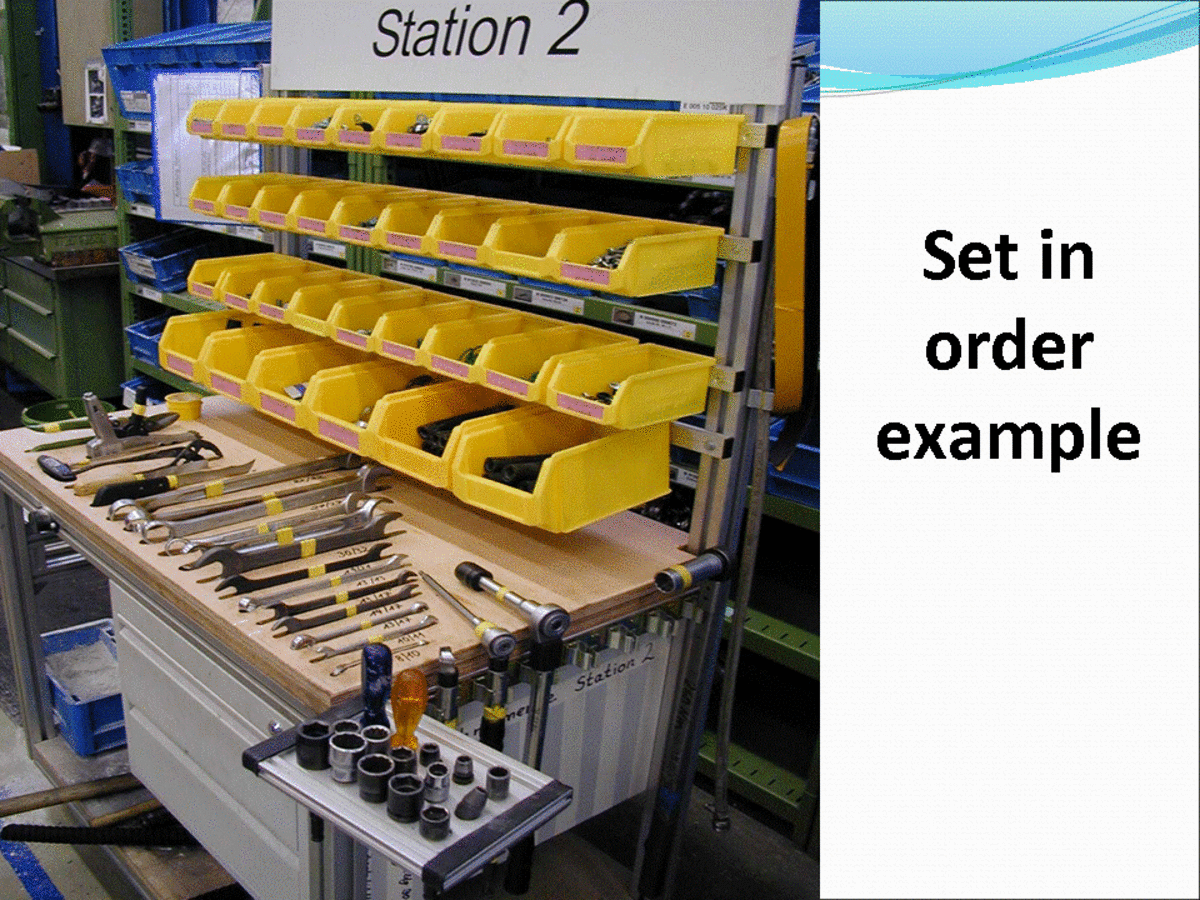
Using The 5 S S Seiri Seiton Seiso Seiketsu And Shitsuke Toughnickel Money
Www Ksre K State Edu Agsafe Announcements Guide 5sp 12 28 17 Pdf

Introduction To The 5s Concept Uttana Com
Www Mdpi Com 71 1050 11 14 37 Pdf
Understanding What Really Happens On A Gemba Walk Planet Lean
Http Www Intracen Org Uploadedfiles Intracenorg Content Exporters Exporting Better Quality Management Assetpdf Bulletin eqm 5s Pdf
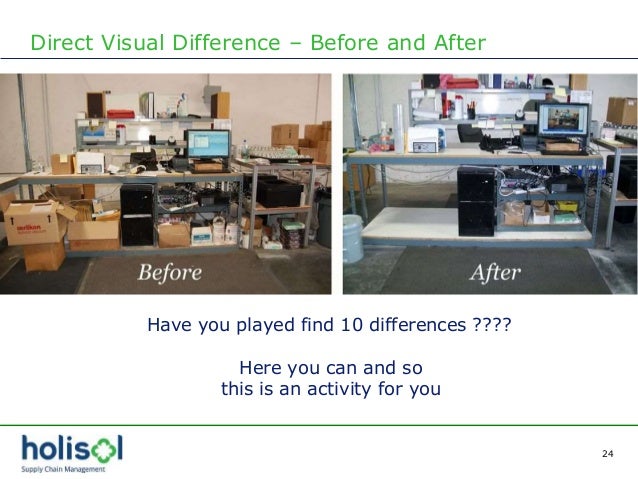
5s Implementation Workshop
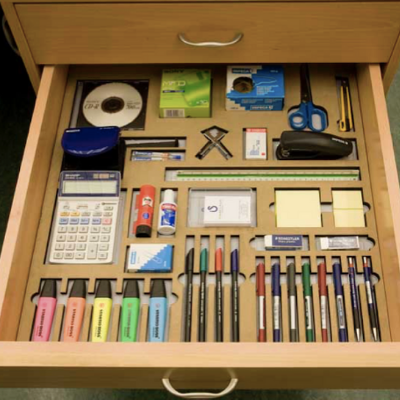
Keys And Tips To Implement The 5s Methodology
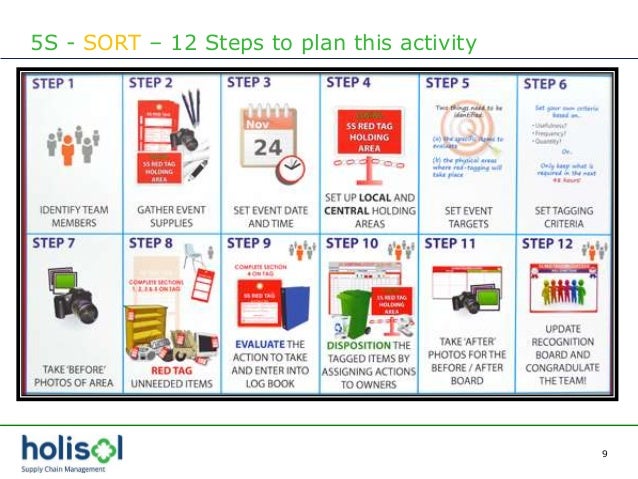
5s Implementation Workshop
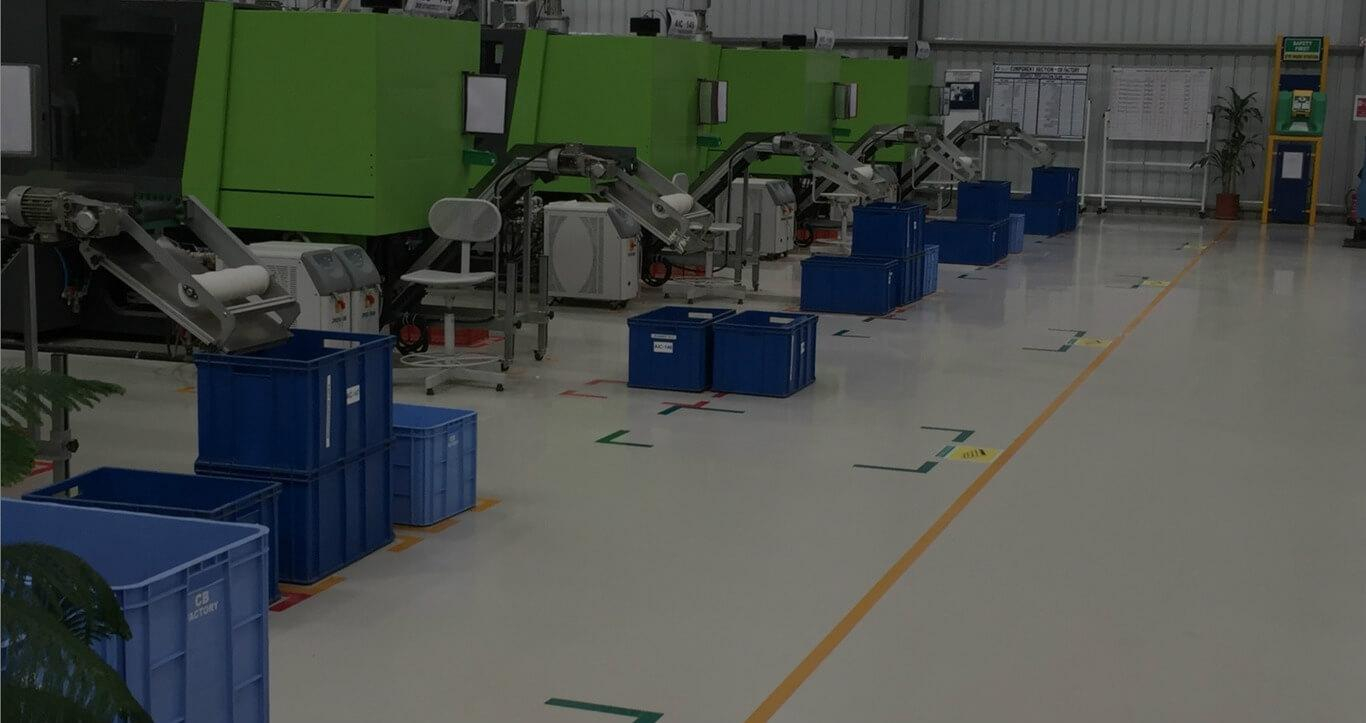
Method 5s Explanations And Example Of The 5s Lean Sesa Systems
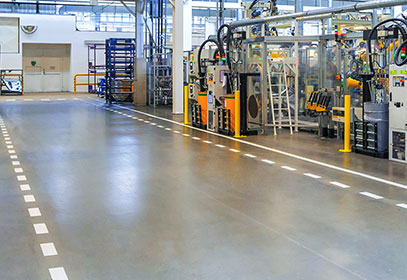
Floor Marking For 5s Creative Safety Supply

What Is The 5s System Definitions Core Concepts Principles Graphic Products
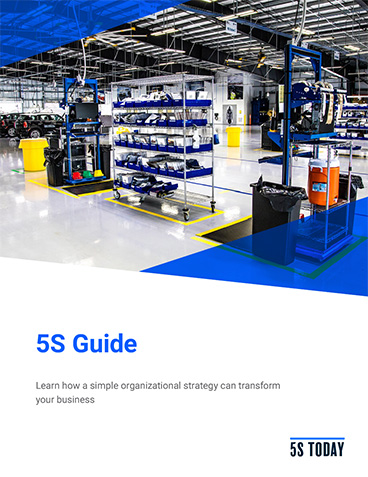
What Is 5s 5s System Is Explained Including Tips On Getting A 5s Program Started

5s Methodology Wikipedia
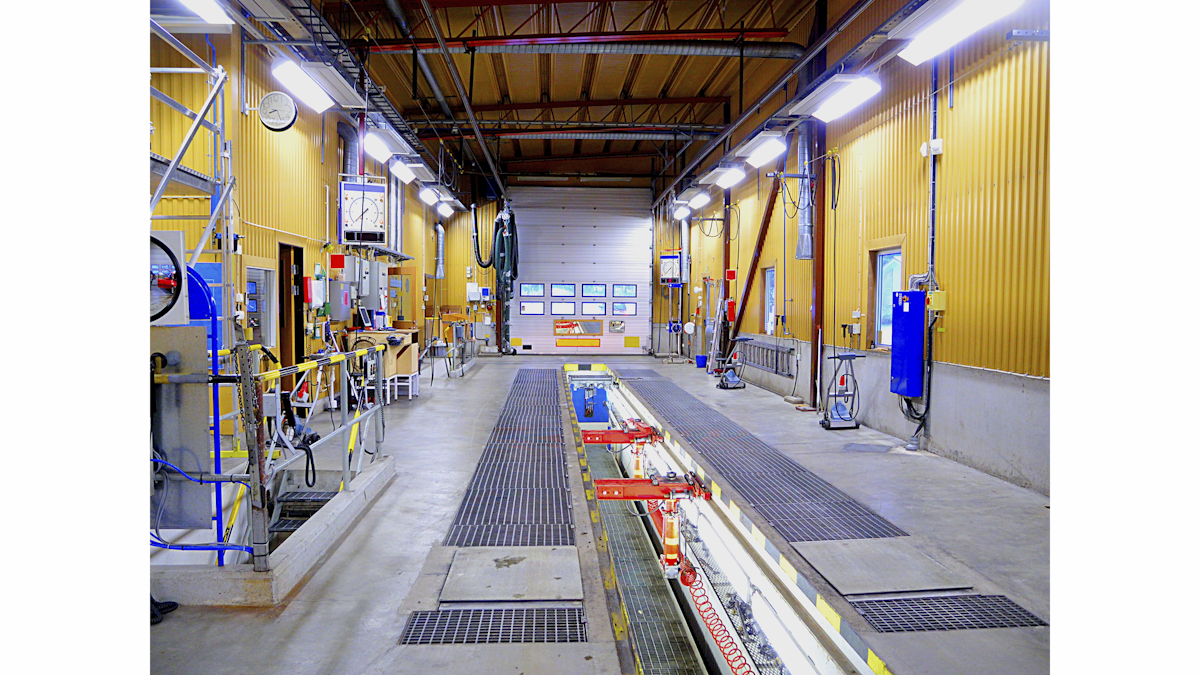
How To Get Your Shop In Order For Safety Process Improvement Fleet Maintenance

5s Work Flow Management In Enterprise Excellence Deployment Bpminstitute Org

Safe Shops Not By Accident Construction Equipment
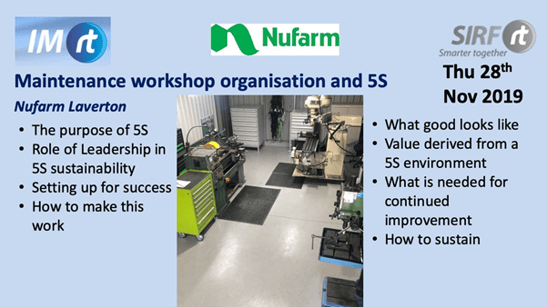
Sustainable 5s In Maintenance More Than Just Sort Straighten Shine Standardise Sustain
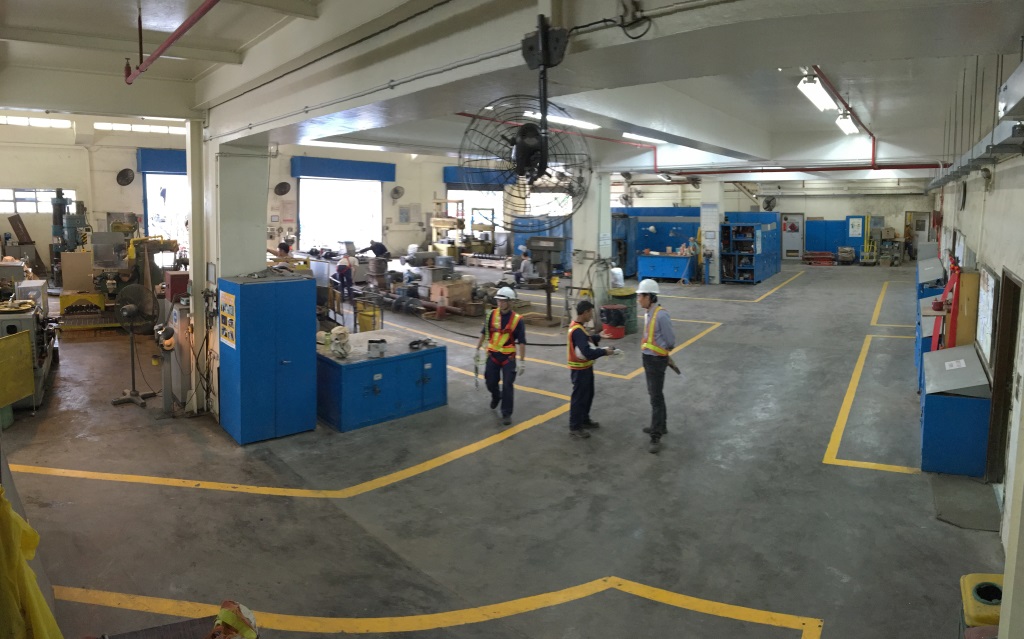
Quality

Training Event 5s For Maintenance Workshop And Store Shopfloor Improvement Specialist
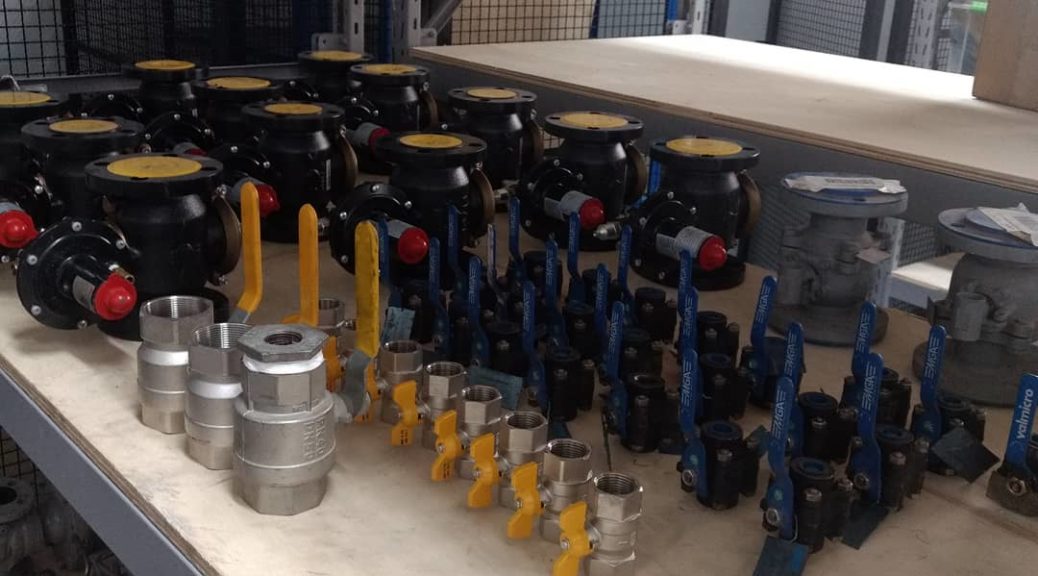
5s Is Applied In A New Sao Paulo Maintenance Workshop Tv Sbobet แทงบอล ออนไลน
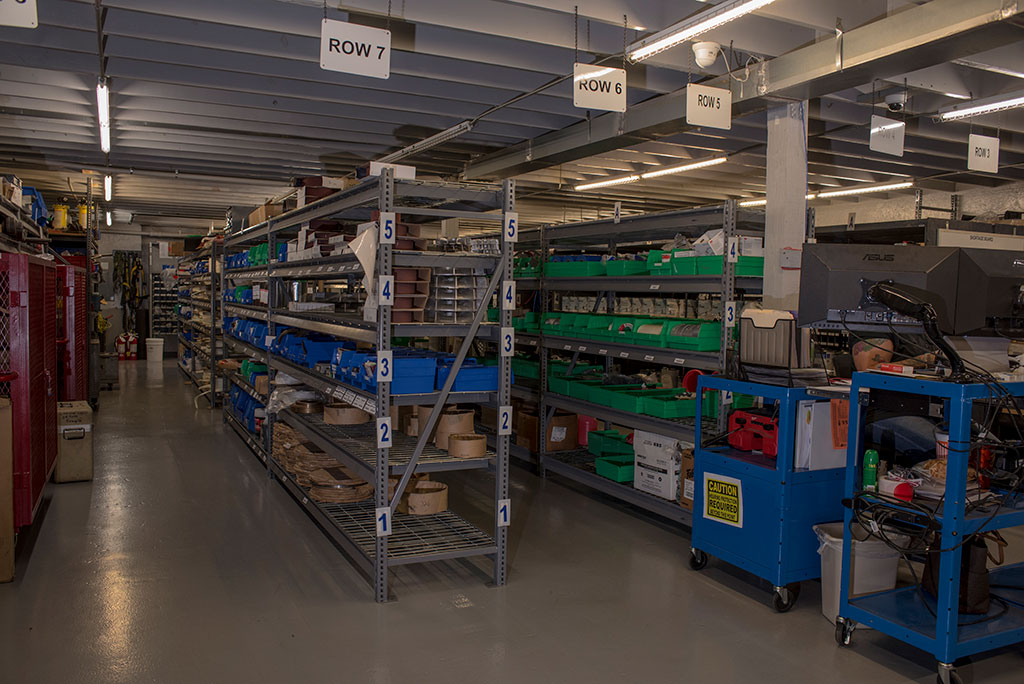
5s Implementation Bradleys Motors Gregory Tx
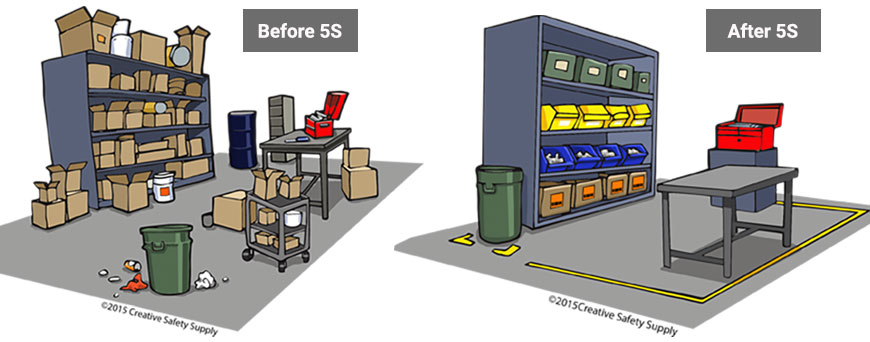
What Is 5s 5s System Is Explained Including Tips On Getting A 5s Program Started

Projects Jamec Equipements Industriels Et Postes De Travail 5s

What Is The 5s System Definitions Core Concepts Principles Graphic Products

Getting Started With The 5s System 5s Implementation Plan Graphic Products

5s Training Course

Tools Drawer At A 5s Working Place Tool Box Organization Tool Drawers Free Woodworking Project Plans

Tools For 5s Lean Manufacturing Process Checklists And More Graphic Products
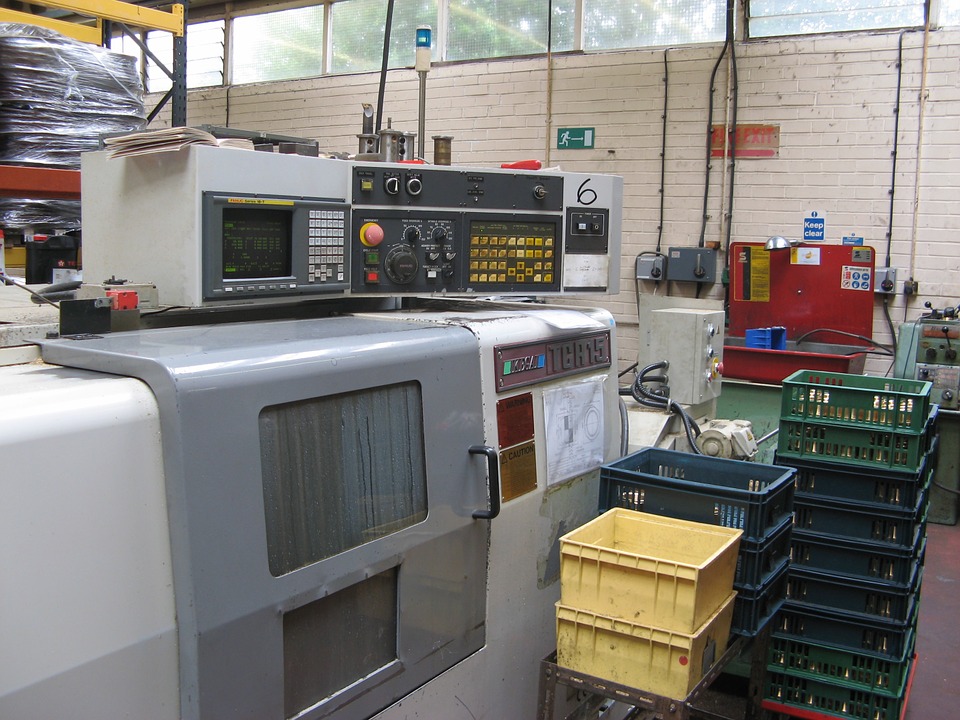
What Is 5s And How Does It Relate To Lean Manufacturing
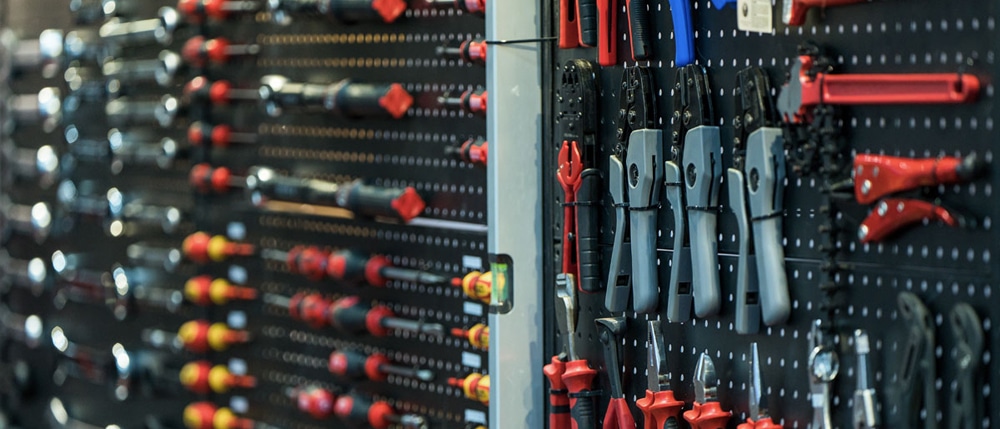
5s Basics Workplace Organization New Hampshire Manufacturing Extension Partnership Nh Mep
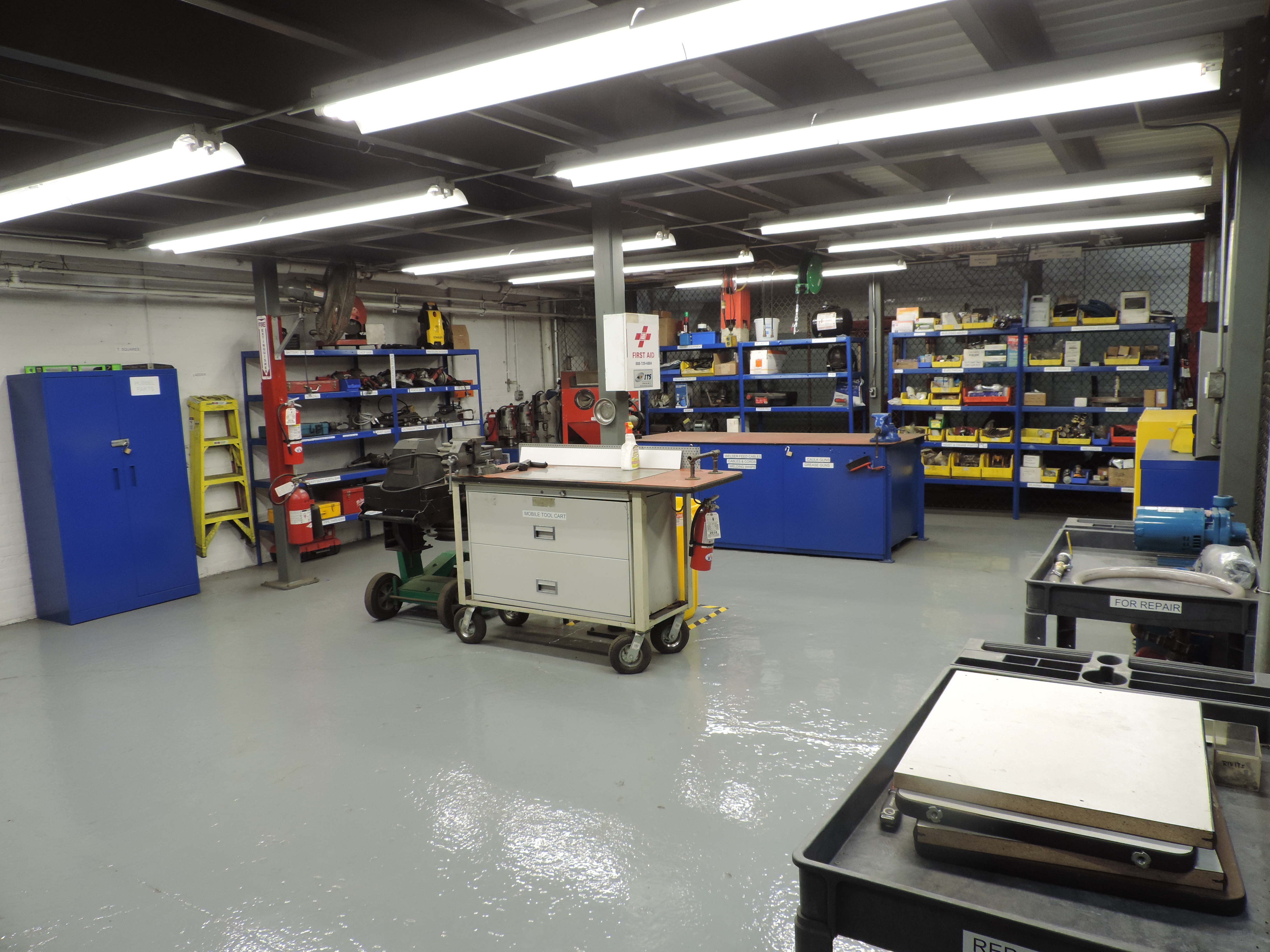
5s Maintenance Its International Thermal Systems
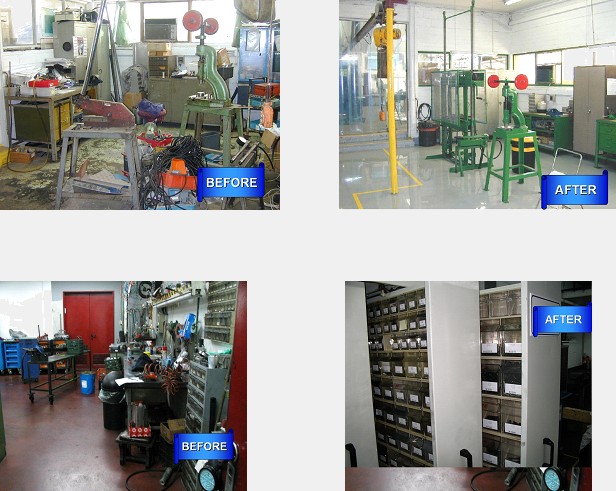
5s
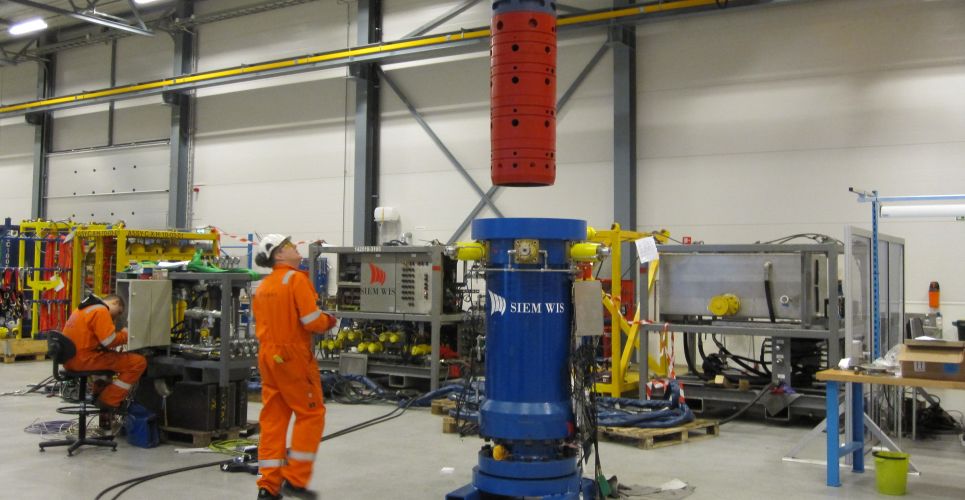
Workshop Wellis Mpcd

5s Lean Programme To Improve Work Efficiency Eu Pig Innovation Group
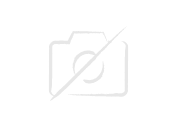
5s Workshop Storage Cabinet 5s Visual Cabinet Sesa Systems
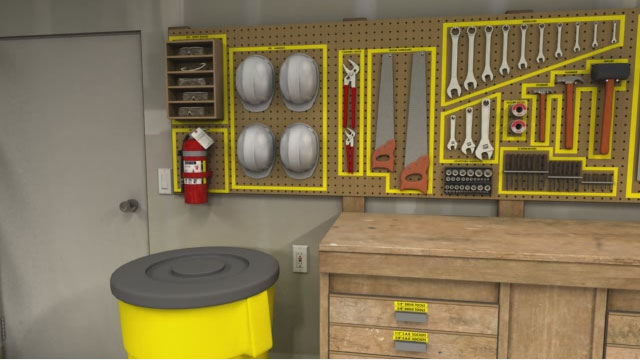
5s Training Course Online 5s Training Video

Projects Jamec Equipements Industriels Et Postes De Travail 5s

Pdf Implementation Of 5s Methodology In A Metalworking Company
Http Www Intracen Org Uploadedfiles Intracenorg Content Exporters Exporting Better Quality Management Assetpdf Bulletin eqm 5s Pdf
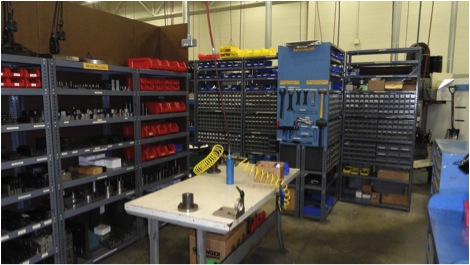
5s Visual Workplace Problems Identified Problems Solved Association For Manufacturing Excellence

Here S How To Optimize And Automate Your Equipment With 5s

Shadow Board Design In Uk By Lean 5s Products Uk Issuu

Impacto De Las 5s En La Productividad Calidad Clima Organizacional Y Seguridad Industrial En La Empresa Cauchometal Ltda

Tps Lean Manufacturing Glossary 5s Visual Workplace Lean Manufacturing Visual Management Lean Sigma

5s Techniques By Operational Excellence Consulting
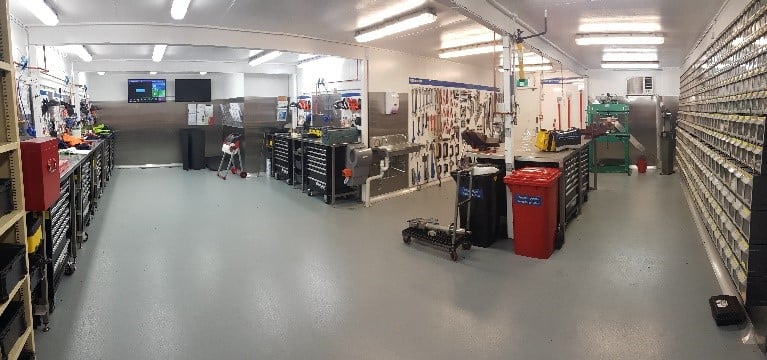
Asahi Maintenance Team Applies 5s
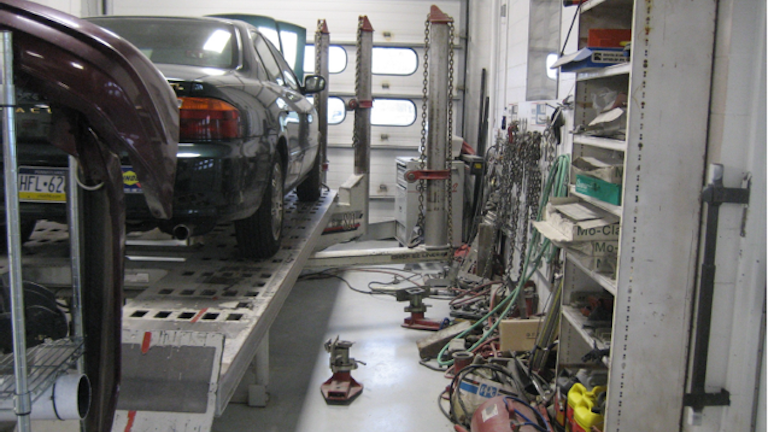
Point Of Use Fleet Maintenance

Applying 5s Series Part I Introduction Reliable And Efficient

What Is 5s And How Does It Relate To Lean Manufacturing
Www Mdpi Com 71 1050 11 14 37 Pdf
Using 5s Methodology To Improve Your Digital Workplace
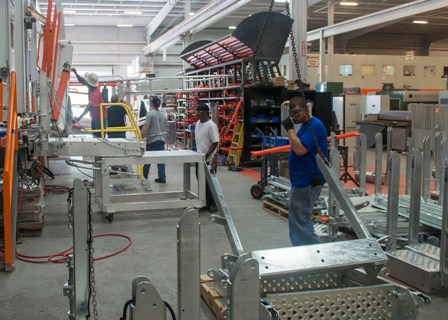
Plant Engineering Safety Is It The Sixth S In A 5s System
Www Mdpi Com 71 1050 11 14 37 Pdf
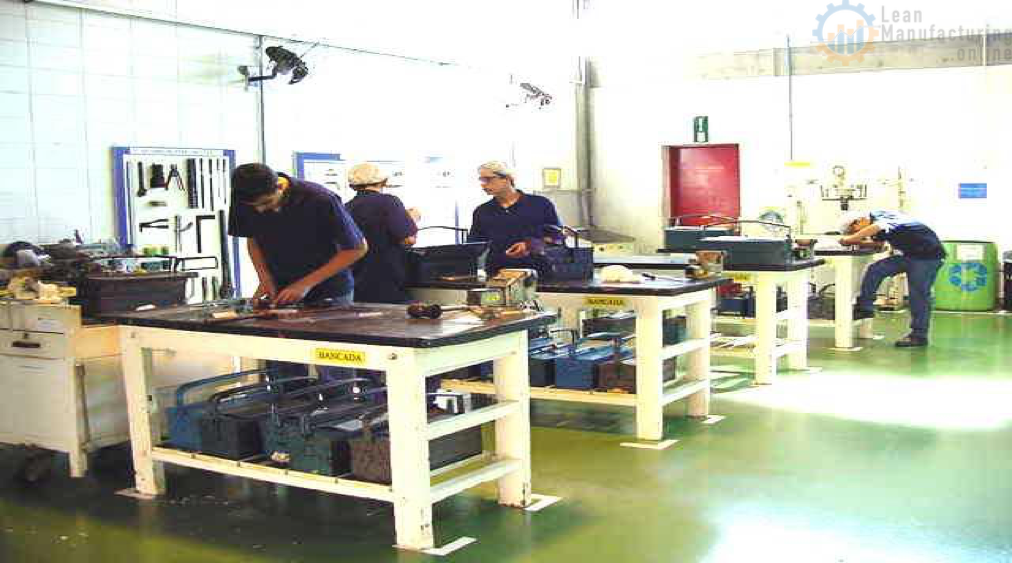
Maintenance Workshop Continuously Improving Manufacturing
Www Advancedtech Com Wp Content Uploads 17 12 Using 5s To Transform The Parts Storeroom Pdf

Agile Lean Business Solutions Albs Hands On Lean Consultants Bangalore India
Q Tbn And9gcthah55 X2dyrsi5szwu47kvvkr8foxqtkfdj3f6nugrl9 Yyi1 Usqp Cau

70 5s Ideas In 21 Lean Manufacturing Visual Management Lean Six Sigma
Http Www Intracen Org Uploadedfiles Intracenorg Content Exporters Exporting Better Quality Management Assetpdf Bulletin eqm 5s Pdf

Extreme Makeover Storeroom Edition Life Cycle Engineering

5s Posters Creative Safety Supply

Pdf Implementation Of 5s Methodology In A Metalworking Company

Pin On 5s

3 Ways Your Organization Can Undertake A 5s Audit Izimage

Implementing 5s In Assembly Plants Implementing 5s In Assembly Plants 12 03 01 Assembly Magazine

Maintenance Old Roots New Routes
Www Ksre K State Edu Agsafe Announcements Guide 5sp 12 28 17 Pdf

Backsafe Mining Mine Spec Materials Handling Solutions Facilities Management Maintenance Workshop Warehouse Backsafe Mining
S3 Amazonaws Com Assets Highways Gov Uk Specialist Information Knowledge Compendium Visual Managementvisual Controls Implementation Pilot 5s In Highways Construction And Maintenance Pdf

Extreme Makeover Storeroom Edition Life Cycle Engineering
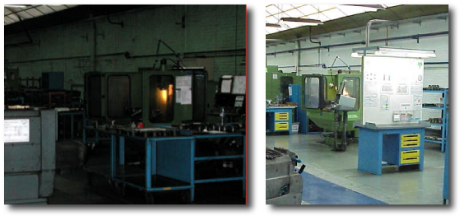
5s Method Housekeeping Factory Systems

5s Methodology Wikipedia
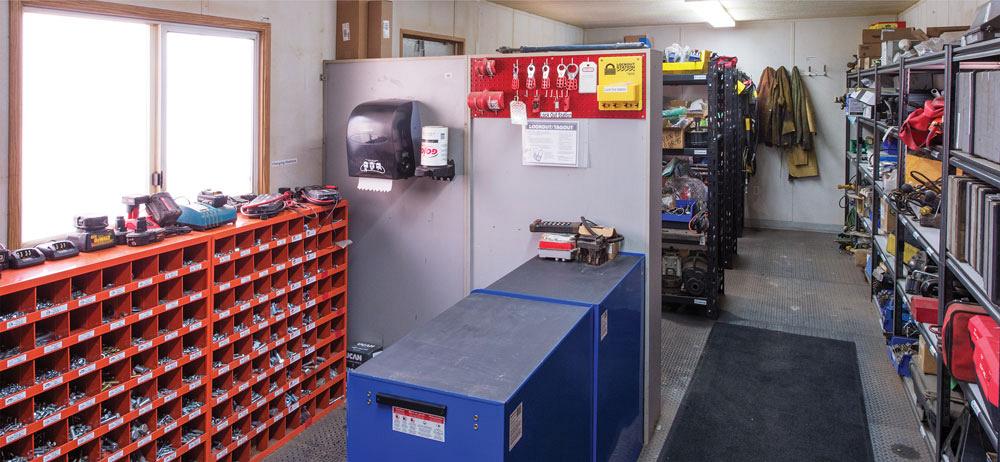
Pdf Separation Anxiety In Children And Adolescents An Individualized Approach To Assessment And Treatment 05
Keys And Tips To Implement The 5s Methodology

The Three Pillars Of Reliable Machine Shop Productivity Modern Machine Shop
3

Autonomous Maintenance

Pin De Lets Go Gemba En Lss Visuals Docencia Organizacion Celulas

5s Lean Resource Center Stop Painting Com
Q Tbn And9gcr8lusywby2j6bkdudrrwiqrov Pyspneufwbrikak Usqp Cau
Victas Imrt Master Class 5s In Maintenance Csf Proteins Laverton Registration Wed 17 02 21 At 10 00 Am Eventbrite